1. Новая марка смолы
Компания "Reichhold", один из крупнейших в мире производителей полиэстеровых смол для катеростроительной индустрии, выпустила новую марку LS своей морской смолы "гидрекс", которая, по словам руководителей компании, выделяет на 65% меньше паров стирена, чем первоначальный продукт.
Новая продукция — смесь винилэстера и смол типа DCPD, сохраняющая гидролизную устойчивость, визуальную объемность профиля и легкость обработки оригинального продукта при пониженном содержании стирена, разработана в США компанией, базирующейся в Research Triangle Park (шт. Северная Каролина) в сотрудничестве с "Toyota Marine Sports" (Гровланд, Флорида), выпускающей мощные буксировщики воднолыжников. "Toyota Marine" использовала гидрекс, но решила снизить выбросы стирена ниже уровня 20 частей на миллион (ppm), не отказываясь от технологии внешнего напыления.
"Toyota" уже строит катера с использованием этого экспериментального материала и довольна его физическими и эксплуатационными характеристиками, внешним видом.
"Мы собираемся начать выпуск модели 2002 года на базе нового материала и на новой строительной площадке, — пояснил технический менеджер компании Макнейл. — Хотя фактически использование этого материала начнется гораздо раньше. Когда мы предложили нашим рабочим попробовать LS в деле, они остались довольны его технологичностью".
Экологические соображения также имеют важное значение для "Toyota", сказал Марк Макнейл: "Будучи производителем автомобилей, "Toyota" — очень "зеленоориентированная" компания. Благодаря использованию в технологии материала LS с малым содержанием стирена мы попадем в десятку самых экологически чистых предприятий во Флориде. Мы используем его везде, даже в изготовлении мелких деталей".
"Toyota Marine" спроектировала свою новую модель под новую технологию, предполагая ламинировать корпуса при помощи LS.
Программа выпуска продукции на базе гидрекса, но с низким содержанием стирена, продолжает раскручиваться. Вслед за LS Reichhold собирается предложить полностью винилэстеровую смолу гидрекс 100LS. Наконец, выпуск гидрекса ONE с пониженным содержанием стирена, но для менее ответственных применений, ожидается в начале осени.
2. Что такое твинтекс?
Первые корпуса из нового материала под названием "твинтекс" на базе термопластика обретают форму в компании "Halmatic" — крупнейшем в Англии производителе коммерческих катеров. Будучи ныне частью группы "Vosper Thornycroft", компания использует технологию, недавно разработанную в стенах Центра композитных технологий этой группы. Сам материал производится французским текстильным предприятием "Saint-Gobian Vetrotex".
Скоро появятся экспериментальные лодки RIB из смеси полипропилена и стекловолокна, которая является армирующей составляющей композита в той же степени, что и в обычном ламинированном стеклопластике. Главное отличие между двумя материалами в том, что вместо пропитки стекловолокон смолой, которая затвердевает в результате химических реакций (случай GRP), в твинтексе пластмасса формируется под воздействием нагрева.
Когда полипропилен и стекловолокно уже смешаны друг с другом, процесс заключается только в укладывании этого материала поверх матрицы. Однако матрица в этом случае существенно отличается от тех, что применяют в производстве корпусов из стеклопластика: она должна и выдерживать нагрев, достаточный для расплавления полипропилена, и служить прочной опорой до тех пор, пока пластик находится в жидкой фазе.
В настоящее время "Halmatic" использует двойные металлические матрицы, но их изготовление обходится дорого и может быть оправдано только при массовом выпуске относительно простых корпусов. Компания ищет альтернативный материал, чтобы сделать экономически оправданным выпуск малосерийной продукции на базе пластика с меньшими температурными "запросами".
Первый серийный корпус, сделанный по новой технологии, это 5метровый армейский десантный катер "Mk VI". При его проектировании предусмотрена возможность компактного штабелирования корпусов при перевозке и хранении. Ширина — 2 м, вес — всего 165 кг (без мотора) при грузоподъемности 1500 кг. Подвесные моторы мощностью от 20 до 40 л.с. обеспечивают скорость 6 узлов. Помимо основного назначения катер может использоваться для эвакуации населения при наводнениях.
Чтобы опробовать новую технологию на более сложных корпусах, компания строит лодку RIB. Матрица относительно проста внешне, но ее конструкцию усложняет то, что внутри корпус имеет ребра подкрепления.
Технология формования твинтекса позволяет достичь большей точности и меньшей себестоимости, чем при использовании технологии GRP Практически нет никаких отходов материала. Корпуса, изготовленные из твинтекса, имеют меньший вес, большую водостойкость и химическую стойкость. При формовании нет выделения вредных веществ. Еще одно важное преимущество состоит в том, что материал полностью поддается вторичной переработке.
3. Стеклосэндвич
Датская компания "Parabeam" предложила параглас — разновидность трехмерной стеклоткани, которая позволяет корпусостроителям выпускать композитные панели за один этап — без последовательного накладывания слоев.
Ткань изготовлена из стеклома-териала E-Glass и представляет собой две параллельные поверхности, связанные вертикальными "столбиками"; данная структура поглощает разогретую смолу за счет капиллярных сил. Затем ткань автоматически разбухает до заранее выверенной величины и представляет собой уже пространственную ламинированную структуру толщиной 3, 5, 8, 10, 12, 15, 18 или 22 миллиметра. Типичное соотношение стеклоткани и поглощенной ею смолы 1:1.1 (для полиэстера, винилэстера) и 1:0.95 (для эпоксидной смолы).
Параглас создан для применения в морской индустрии, главным образом — изготовления мостиков, переборок, подволока кают, пола и легких выгородок. Одноэтапность изготовления дает существенную экономию времени, исключен риск расслоения готовой конструкции. Еще одно преимущество — простота декоративной отделки (по словам разработчиков), а также повышенное соотношение прочности к весу, повышенная жесткость панелей, более привлекательный внешний вид. Риск коробления и изломов практически исключен.
4. Палочка-выручалочка?
Второе поколение материалов с предварительной пропиткой открывает новые возможности для морской индустрии. Система SPRINT английской компании "SP Systems" должна стать поворотным моментом в развитии слоистых материалов.
Долгие годы в корпусостроении доминируют материалы с предварительной пропиткой (пенные и ячеистые), дополненные технологией вакуумного формования. И сейчас эти "перспективные" композитные материалы используются в основном при строительстве высококлассных яхт на заказ. Однако их применение в массовом строительстве ограничено, главным образом ценой. Композитные материалы не только дороги сами по себе, но и требуют дорогой технологии. Ламинизация таких материалов — куда более трудоемкий процесс, чем простое "мокрое" накладывание слоев обычного стеклопластика. И, главное, — более длительный.
Сложность процесса можно преодолеть применением разного рода технологической оснастки, но средств ускорить процесс предварительной пропитки нет. Приходится не только терпеливо накладывать один на другой тонкие слои, да еще и удалять попавшие в материал пузырьки воздуха. В деталях, которые должны иметь значительное поперечное сечение (например, мачта из углепластика), приходится вручную накладывать 60 слоев и более! А после этого еще следуют стадии вакуумного формования и затвердевания. Даже обычная корпусная конструкция требует как минимум трех этапов ламинизации — вакуумное формование и сушка первого слоя из углепластика; нанесение пенного заполнителя на сотовую структуру в качестве среднего слоя и снова формование и сушка верхнего слоя из углепластика. В зависимости от типа подкрепляющих конструкций и тканей толщина одного слоя колеблется от 0,1 до 1,5 мм. Толстые слои труднее наносить по огибающим кривым и углам.
Новая технология получила название SPRINT, что, помимо скорости, обозначает аббревиатуру SP Resin Infusion Technology.
Ткани SPRINT отличает то, что это — материал предварительного изготовления и предварительной катализации. Обычные материалы предварительной пропитки представляют собой вязкую пленку смолы, которой пропитана усиливающая структура из волокон. SPRINT — это готовый к употреблению сэндвич из волокон и смолы, то есть пленка смолы между двумя наружными сухими слоями из армирующих волокон.
Это — абсолютно сухой на ощупь материал, но если сжать поверхности с достаточной силой, смола начнет просачиваться наружу. При формовании корпуса из этого материала его можно накладывать, перемещать, разглаживать, что делает процесс точным и быстрым. Обычные материалы с пропиткой (особенно — более толстые и тяжелые) жестче, поэтому их труднее наложить точно так, как необходимо. Материалы SPRINT, даже будучи раза в два толще обычных, более эластичны, поэтому из них можно формировать поверхности сложной геометрической формы, загибать в углах. От рабочих не требуется столь высокой квалификации. Поскольку выходу пузырьков воздуха наружные поверхности не препятствуют, нет нужды ни в прессовании, ни в применении автоклава.
Требования к сушке изделия почти не отличаются от стандартных. При нагреве пленка смолы размягчается и легко просачивается через наружные слои. Величина отходов крайне низкая — обычно не более 0,5%.
При аналогичных весовых и прочностных характеристиках материалы SPRINT не дороже или даже несколько дешевле обычных.
Варианты материалов в принципе те же, что и обычно: уголь, стекло и арамиды. Похожи и варианты структуры армирующих слоев: хаотическое расположение волокон, тканые материалы, плетеные материалы, "кочующие" плетения или разные варианты многоосной ориентации волокон.
Один из вариантов материала — SPRINT CBS с одноэтапной технологией формования — разрабатывался для автомобильной промышленности, но может успешно применяться и в морской индустрии. Этот уникальный материал имеет наружные поверхности из углеволокна с очень тонким и прочным средним слоем, благодаря чему после герметичной сушки становится эквивалентным по жесткости листу стали толщиной 1 мм, но при этом на 3/4 легче его. Применение SPRINT CBS снижает вес компонентов из "твердого углеволокна" на 20%.
В общей сложности, по словам работников "SP", время технологической обработки материалов SPRINT вдвое меньше, чем обычных материалов с предварительной пропиткой. Компания рассчитывает на то, что ее технология привлечет внимание "композитных" клиентов верхнего ценового уровня своими преимуществами -меньшим весом, повышенной прочностью и жесткостью, повышенной структурной целостностью, не говоря уже о славе более экзотической конструкции корпуса при вполне умеренной цене готового изделия.
Финская верфь "Nautor", известная строительством самых элегантных яхт типа "Swan", начала экспериментировать с материалами SPRINT. Пока это всего лишь палуба для "Swan-45".
Технология пока еще отработана недостаточно — чревата ошибками с удалением пузырьков воздуха, выбором температуры и длительности сушки. Наиболее показательный пример — авария композитного сверхскоростного парусного катамарана Пита Госса "Team Philips", не считая ряда аварий претендентов на Кубок Америки, ставших жертвой слишком далеко зашедшего компромисса между прочностью и весом. "Team Philips" потерял одну из двух носовых оконечностей еще во время первых ходовых испытаний. Проблема оказалась не в проекте, а в элементарной ошибке в ходе ламинирования корпуса.
При формовании корпуса с наполнителем "пчелиные соты" надо отдавать себе отчет, что будет, если в одной из ячеек останется пузырек воздуха. Во время сушки (обычно при температуре 80°С) пузырек начнет расширяться и может легко разорвать связь между наружным и внутренним слоями, причем визуально это заметить трудно. Именно это и имело место в стрингерах "Team Philips". Решение проблемы — инструментальное прокалывание обшивки до сотовой структуры на этапе, предшествующем сушке, чтобы отсосать весь воздух.
Аналогичные проблемы встречаются и в случае применения пенных материалов типа поливинилхлорида, но здесь корень зла -не только пузырьки воздуха, но и выделяемые в результате химической реакции газообразные вещества, препятствующие нормальному течению процесса затвердевания смол. Именно поэтому "SP" сейчас ищет более стабильную альтернативу поливинилхлоридным материалам.
Еще одна крупная неприятность произошла с одним известным европейским строителем яхт. На верфи был явно нарушен температурный режим сушки и материал не затвердел должным образом. В результате в отходы был списан целый 100-футовый корпус, и пришлось начинать все с нуля. Сама технология горячей сушки — это еще одна головная боль. Будь то сушка печью или в "горячей" комнате, по всему корпусу надо установить датчики температуры, чтобы быть уверенным в равномерном распределении температуры.
Отрицательный опыт и циркулирующие "страшилки" заставляют многих отказываться от риска и использовать более простые и безопасные привычные технологии. Однако тот, кто учится на ошибках, делает меньше ошибок, чем это кажется со стороны.
Первое судно из материала "SPRINT" было недавно построено в Англии компанией "Green Marine". Это спасательное судно с быстрым спуском на воду для национальной службы спасения (RNLI). Судно сейчас достраивается на верфи "Devonport Yachts". На этой же верфи идет пока секретное строительство большой моторной яхты с надстройкой из углепластика. Принято считать, что "экзотическими" материалами должны заниматься относительно мелкие специализированные фирмы, такие как "Green Marine". Но как знать, не изменятся ли эти взгляды с появлением материалов SPRINT? При том, что над обычной технологией "мокрого" формования нависает Дамоклов меч экологических ограничений, именно SPRINT может стать столбовой дорогой в будущее.
5. Звездное качество
Передовая голландская яхтенная верфь "Royal Huisman Shipyard" — пионер в применении нового прочного коррозионностойкого алюминиевого сплава Alustar, разработанного исследовательской компанией "Corus". Все яхты, построенные на верфи в Волленхове, неподалеку от Амстердама, сделаны именно из этого материала.
Информация об изображении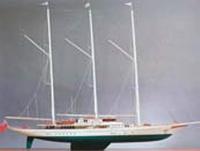
Крупнейшая в мире алюминиевая 90-метровая шхуна "Athena" из нового сплава Alustar
Недавно верфь выпустила первые две яхты из нового материала. Одна из строящихся яхт будет крупнейшей в мире алюминиевой яхтой, а также крупнейшей частной парусной яхтой. Это 90-метровая трехмачтовая шхуна "Athena", спроектированная Джерри Дийкстра и Питером Билдснийдером. Она должна быть сдана главе фирмы "Nerscape" доктору Джиму Кларку в сентябре 2004 года.
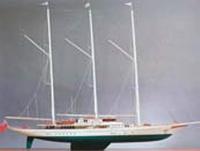
Крупнейшая в мире алюминиевая 90-метровая шхуна "Athena" из нового сплава Alustar
Уже построенные из нового материала яхты — 34-метровый куттер "Pamina" с палубным салоном (проект Теда Худа) и 34-метровый шлюп "Unfurled" (проект бюро Германа Фрерса). Помимо яхты "Athena" строится 50-метровая классическая шхуна "Borkumriff IV" (проект Джерри Дийкстра и Джона Олдена), а также 40-метровый элегантный классический шлюп Брюса Кинга "Cecilie-Marie".
Alustar первоначально разрабатывался для быстроходных паромов.
Фактически, по сравнению с АА5083, новый материал прочнее на 26% до сварки и на 28% после нее, что выражается в абсолютных цифрах как 160 ньютонов на квадратный миллиметр для Alustar и 125 для АА5083.
Что касается коррозии, обширные испытания не выявили никаких ее признаков, тогда как при тех же условиях АА5083 имел явные признаки питтинг-коррозии. Внутригранулярная коррозия у Alustar также значительно ниже, чем у АА5083.
В отношении технологичности Alustar также не имеет никаких изъянов. Г ибкость и свариваемость у обоих сплавов одинаковая, хотя некоторые изменения в технологию внести все же пришлось.
"Сварка Alustar требует немного большей силы тока, чтобы компенсировать большее количество магния в сплаве. Кроме того сваривать надо немного быстрее, чтобы избежать коробления", — говорит Питер Акербум, менеджер верфи.
На данный момент используются те же проволочные электроды, что и для АА5083, однако "Corus" уже разрабатывает новую электродную проволоку.
Верфь экспериментирует со сваркой в аргоновой среде, которая не везде популярна. "Некоторые утверждают, что сваривать лучше в гелиевой среде, но у нас и с аргоном никаких проблем, — говорит Акербум.
Что касается стоимости материала, Alustar всего на 8% дороже АА5083. Новый материал был создан Алюминиевой ассоциацией под маркой АА5059 и поставляется в листах тех же размеров, что и предшественник.
Для проектантов яхт новый материал оставляет выбор: делать суда более прочными или более легкими при заданной прочности. Коррозионная стойкость также имеет большое значение для верфи, имеющей репутацию строителя лучших в мире парусных яхт.
Для гигантской яхты "Athena" повышенная прочность нового материала имеет особое значение. Благодаря экономии веса водоизмещение составило всего лишь около 1000 тонн, и даже все три мачты будут сделаны из этого материала (хотя реи и гафели будут из углепластика). Корпус будет обшит листами марки Alustar-H321, а набор корпуса образован штамповкой из Alustar-H112. Толщина обшивки в основном 10 мм (ниже ватерлинии), и 12 мм в носовой части, подвергающейся ударам волн.
Всю весну и лето на верфи трудились над килем яхты, в котором разместится большая часть балласта (217 тонн). Толщина обшивки киля 15 мм, шпунтового пояса — 20 мм.
Дальнейшую работу тормозит перестройка эллинга: высота яхты составит 77 м! После спуска на воду придется разобрать местный мост, чтобы могла пройти яхта шириной 12,2 м; для проводки по каналам ее придется ставить на понтоны, поскольку осадка 5,5 м — больше глубины канала.
В двух других проектах, "Pamina" и "Unfurled", верфь пошла по пути компромисса - умеренного увеличения прочности и столь же умеренной экономии веса. Экономия веса по корпусу и надстройке "Pamina" составит лишь 5%. В целом яхта вполне укладывается в требования Ллойда для судов из металлических сплавов. Например, толщина обшивки будет такой же, как и для сплава М5083, - 5 мм выше ватерлинии и 6-7 мм ниже. Общий вес корпуса и надстройки составит 25,5 тонн, в киль будет уложен свинцовый балласт весом 33,3 тонны.
Тем временем в Германии "Corus" уже наладила выпуск готовых палубных секций из Alustar под названием Coraldec. Это соединенные лазерной сваркой плоские листы с гофрированным листом между ними. Главные преимущества таких панелей — уменьшенные на 25% вес и толщина в сравнении со стандартными секциями из листов и подкрепляющего набора.
6. Основа для эпоксидных материалов с предварительной пропиткой
Шведская компания DIAB — производитель материалов для строительства стеклопластиковых корпусов, создала пенный материал, предназначенный специально для использования с эпоксидными смолами. Этот новый материал называется Divinycell HPS и отличается великолепной стабильностью при температурах до 120°С. Кроме того, он совместим с режимами сушки подавляющего большинства применяемых ныне эпоксидных смол.
По мнению компании, применение HPS расширит сферу применения "сэндвичевых" композитных конструкций. К тому же материал дешевле, нежели материалы типа "пчелиные соты", и избавляет производителей от вредного для здоровья процесса послойного накладывания "мокрых" материалов.
Вдобавок к стойкости к высокотемпературным процессам формования корпуса, Divinycell HPS — столь же стоек и к эксплуатационным условиям: выдерживает температуру 90°С.
Пока материал выпускается в трех градациях плотности: 80, 100 и 130 кг/м3. Другие марки появятся при наличии рыночного спроса. Механические свойства нового материала, по словам фирмы, не хуже, чем у Divinycell H, наиболее продаваемого сегодня пенного материала.
По сравнению с другими материалами марки Divinycell, новинка отличается легкостью обработки обычными столярными инструментами — его можно сверлить, пилить, фрезеровать, обрабатывать на токарном станке с малыми допусками. Материал поставляется в листах, а также готовыми наборами для серийного производства. В последнем случае заказчик получает комплекты вырезанных и пронумерованных деталей, готовых для сборки в матрице будущего корпуса. Такой подход позволит существенно снизить затраты времени, рабочей силы и снизит количество отходов.
7. Крупнейший в мире композитный корабль
Шведские ВМС проводят ходовые испытания многоцелевого корвета "stealth" "YS2000" класса "Visby". При длине 73 м и ширине 10,4 м это крупнейшее в мире судно с композитной конструкцией типа "сэндвич".
Корвет построен на верфи "Kockums AB" в Карлскруне. Это первый корвет из шести заказанных шведскими ВМС.
Предусмотрены все меры для уменьшения электромагнитного поля корабля, в том числе применена пассивная композитная технология "stealth", первоначально испытанная на 30-метровом тестовом судне "Smige". Корпус, палуба и надстройка имеют большие плоские поверхности с острыми углами, большинство палубных механизмов спрятано под палубой для снижения радарного силуэта корабля. Инфракрасный след уменьшен за счет вывода отходящих газов через отверстия в носу, расположенные близко к ватерлинии.
В прошлом для корпусов и палуб тральщиков использовалась одинарная ламинированная композиция стеклопластик/полиэстер, которая хотя и была немагнитной, отличалась большим весом. Теперь применен сэндвич с серединой из "DIAB DivinycellR" и наружными слоями углепластика и винилэстера для максимизации соотношения прочности к весу при сохранении низких магнитных свойств. Винилэстер "Norpol Dion" поставляется американско-норвежским предприятием Reichhold.
Менеджер проекта Сен-Эрик Хелбратт сказал, что "выбор материалов определялся требованием малого веса, мы достигли этого путем использования поливинилхлоридной пены в качестве наполнителя между слоями винилэстера, усиленного углепластиком. Это обеспечило конструкцию с высокой статической прочностью и сопротивляемостью нагрузкам".
Различные конструкции собираются из плоских панелей, изготовленных по технологии вакуумного вливания, специально разработанной на верфи под данный проект. Затем панели соединяются в секции.
Чтобы ускорить процесс и минимизировать отходы была специально разработана основа слоистой конструкции — "DivinycellR" (первоначально — высокой плотности), предварительно выпускаемая на заводе Laholm компании DIAB (Швеция) в виде листов размером 13,5x2,5 м и толщиной до 90 мм. Листы еще на заводе снабжаются решетками для облегчения процесса вакуумного вливания и перевозятся в Карлскруну на специальных широких трейлерах.
Владелец предприятия, которое строит композитные суда из стеклопластика уже 25 лет, утверждает, что "не видит причин, почему нельзя будет в ближайшем будущем строить композитные суда длиной до 150 метров".