1. Винилэфирные смолы эпоксивинилэфир
Norpol CorVe эпоксивинилэфиры являются термостойкими смолами, разработанными для применения в производстве армированных композитов. Они представляют собой идеальный продукт для применения в изделиях, к которым предъявляются повышенные прочностные требования, где предполагаются высокие статические или динамические нагрузки и, в особенности, при работе в химически агрессивных средах. Изделие из эпоксивинилэфирных смол обладает повышенной стойкостью к поверхностному растрескиванию и образованию глубинных трещин.
Norpol CorVe эпоксивинилэфиры демонстрируют более высокие прочностные характеристики, что и эпоксиды, но при этом более доступны по ценам и проще в применении. Композиты с их применением обладают высокой усталостной прочностью и низким водопоглощением. Комбинация всех этих качеств дает композитам на базе Norpol CorVe преимущества перед такими распространенными материалами, как сталь и алюминий. Высокие пластические свойства смолы в процессе нанесения на матрицу обеспечивают свободу в выборе дизайна. Композиты на основе винилэфирных смол хорошо проявили себя в производстве лопастей ветряных турбин, в авиационном и транспортном секторах, а также в производстве корпусов судов, плавательных бассейнов и ванн "жакузи".
Базовые эпоксивинилэфиры Norpol CorVe:
- 8300. Наиболее универсальная эпоксивинилэфирная смола, обладающая исключительно высокой химической стойкостью, особенно к кислотам, щелочам и окисляющим агентам, хорошей жесткостью и высокими усталостными характеристиками; обеспечивает хорошую адгезию с армирующим волокном;
- 8100. Эпоксивинилэфирная смола с вязкостью ниже, чем у 8300, но обладающая в отвержденном состоянии теми же механическими свойствами и химической стойкостью. Низкая вязкость делает эту смолу наиболее удобной для применения в таких процессах, как центробежное литье и пультрузия. Наиболее типичные изделия из 8100 — это лопасти ветряных турбин, небольшие емкости, решетки и настилы технических сооружений;
- 8440. Огнестойкая эпоксивинилэфирная смола. Добавленные в ее состав 3-5% окиси сурьмы дает исключительно высокие показатели огнестойкости Механические характеристики и химическая стойкость те же, что и у 8300. Применяется, когда требуется комбинация огнестойких и химически стойких свойств. Типичные изделия — дымоходы, трубопроводы и короба» ним, а также настилы и дорожки морских и наземных нефтедобывающих станций;
- 8710. Смола, имеющая более высокую температуру тепловой деформации, исключительно высокую химическую стойкость, даже при повышенных температурах. Часто используется в качестве внутренней облицовки крупных емкостей, в производстве стройматериалов, трубопроводов, коробов, решеток и настилов;
- 8770. Смола, эквивалентная 8710, но с еще более высокой температурой тепловой деформации. Наиболее типичные изделия — короба для вытяжки газов;
- 8730 Смола с высокой температурой тепловой деформации и хорошим относительным удлинением, обладающая превосходными показателями химической стойкости и хорошими эксплуатационными характеристиками при высоких температурах, обладает особой стойкостью к хлорированной среде и растворителям. Наиболее типичные изделия — емкости, дымоходы;
- Х185. Модификация смолы с высоким показателем относительного удлинения и исключительно высокими показателями ударной вязкости, низкой усадкой и особенно хорошей адгезией со стекловолокном, кевларами, поливинилхлоридной (PVC) пеной, сталью и бетоном. Эти свойства в комбинации с хорошей химической стойкостью делают эту смолу чрезвычайно удобной для применения в качестве грунта и в производстве конструкций, подвергающихся динамическим нагрузкам.
ОТВЕРЖДЕНИЕ. При комнатной температуре — лучшей системой отверждения в большинстве случаев является Co/DMA/МЕКР (октоат кобальта/диметиланилин/метилэтилкетонпероксид).
В качестве катализаторов для этих смол прекрасно себя показали различные типы МЭКП: Norpol Катализатор №11 ("Jotun Polymer"); Butanox LPT ("Akzo Nobel"); Interox MEKP-LA-1 ("Peroxide Chemie"); Luperox DND ("Elf Atochem"). Но в любом случае, прежде чем приступать к процессу производства, следует произвести испытания выбранного типа МЭКП на время желатинизации.
АКСЕЛЕРАТОРЫ - СО/DMA. При использовании 1 %-ного раствора октоата кобальта рекомендуется добавлять его не более 4% от объема смолы. При нормальных условиях производства для получения оптимального отверждения рекомендуется 0.2-0.5% ДМА( 10%-ного раствора). Это особенно важно, когда речь идет о производстве тонких слоев и тонких ламинатов. При повышенных производственных температурах (свыше 25'С) количество DMA может быть уменьшено или сведено к нулю, так как повышенная температура обеспечивает полное отверждение. При производстве толстых ламинатов ("мокрый-на-мокрый", свыше 5 мм) предпочтительно исключать добавление DMA, поскольку в этих случаях полное отверждение достигается благодаря теплу, выделяемому в ходе экзотермической реакции. Для получения полного отверждения не следует допускать падения температуры в помещении ниже 18°С.
ОТВЕРЖДЕНИЕ ПРИ ПОВЫШЕННОЙ ТЕМПЕРАТУРЕ. Для отверждения эпоксивинилэфирной смолы при повышенной температуре могут использоваться те же катализаторы, что и для полиэфирных смол.
При добавлении 2-4% раствора бензолпероксида (БПО) процесс полимеризации займет несколько дней, однако при температуре свыше 80’С можно получить ускоренное отверждение. Для достижения оптимальных свойств, а также сокращения времени отверждения рекомендуется применение комбинаций катализаторов.
ПОСТОТВЕРЖДЕНИЕ. Для достижения оптимальных механических свойств и химической стойкости, которых можно ожидать от винилэфирного композита, продукт обычно подвергается постотверждению при повышенных температурах: 24 часа при 60°С или 48 часов при 50°С. После этого, изделие должно быть обработано горячей водой (70-80°С) в течение 2 часов и затем промыто в горячей воде, содержащей соответствующее моющее средство. Поверхность должна быть тщательно обработана жесткой щеткой или очищена высоким давлением, а затем промыта еще раз горячей водой. Это процесс следует повторить один или два раза. В заключение изделие следует тщательно прополоскать в чистой воде с тем, чтобы удалить остатки моющего средства. В целях экономии времени можно применять более высокие температуры, однако температура должна повышаться и понижаться постепенно во избежание появления термических напряжений в структуре.
ЗАМЕДЛЕНИЕ РЕАКЦИИ КИСЛОРОДОМ ВОЗДУХА. Смолы склонны к замедлению реакции полимеризации под воздействием кислорода воздуха аналогично тому, как это происходит с обычными ненасыщенными полиэфирными смолами. Для снижения или исключения этого эффекта можно добавлять 2%-ный раствор воска Norpol 9872 в смолу, используемую в верхнем слое.
АРМИРУЮЩИЙ МАТЕРИАЛ. Эпоксивинилэфирные смолы совмещаются и обеспечивают превосходные адгезионные показатели с широким перечнем стекло-, угле- и органических волокон. В результате можно получить ламинаты с превосходной прочностью, высокой жесткостью и прочностью на срез.
2. Поликор
Поликор — это нетканый материал из непрерывного полиэфирного волокна, использующийся как наполнитель и противо-складочный слой в изделиях из стеклопластика, снижающий содержание смолы в ламинате благодаря имеющимся в его структуре микробаллонам — микросферам.
Поликор одобрен Регистром Ллойда для использования при изготовлении корпусов, палуб, надстроек.
Фактический вес стеклопластика, изготовленного с использованием поликора, на 50% меньше, чем стеклопластика, армированного одним стекломатом. При этом стеклопластик с поликором более прочен, чем традиционный, при том же весе; к тому же, значительно снижается эффект отпечатывания фактуры стеклонаполнителя.
Так, например, при ламинате толщиной 1 мм с применением стекломатов вес 1 кв.м получается равным 1500 г (450 г — стекломат, 1050 г — смола), а при использовании поликора — всего 710 г (60 г — поликор, 650 г — смола).
Удельный вес поликора — порядка 0.4 г/см3 при 45%-ном содержании микросфер. Обладая превосходной смачиваемостью, поликор впитывает порядка 55% полиэфирной смолы по объему, при этом никаких изменений по толщине слоя после отверждения не происходит.
ПОЛИКОР: имеет превосходную смачиваемость; превосходно кроится и легко формуется, что делает его незаменимым при выклейке сложных частей изделий, придавая им малый вес и жесткость; придает изделиям высокую ударную прочность; обеспечивает повышение прочности на растяжение и изгиб; дает экономию в весе свыше 50%, уменьшает количество потребляемых материалов и общую стоимость изделия; уменьшает усадку и улучшает теплоизолирующие свойства изделий;обладает способностью препятствовать отпечатыва-нию на гелькоуте структуры стеклоткани первого слоя; обеспечивает равномерную толщину ламината; может быть использован в качестве подготовительного слоя под бальзу или пенопласт.
НЕКОТОРЫЕ РЕКОМЕНДАЦИИ ПО РАБОТЕ С ПОЛИКОРОМ. Приемы работы аналогичны работе со стеклонаполнителями. При использовании Т1000 и Т2000 необходимо нанести 20-30% смолы (см .таблицу) на предыдущий слой стеклонаполнителя, затем уложить поликор и нанести остатки смолы; после этого все прикатывается обычным способом. Необходимо внимательно следить за правильным смачиванием поликора и отсутствием пузырей между ним и предыдущим слоем.
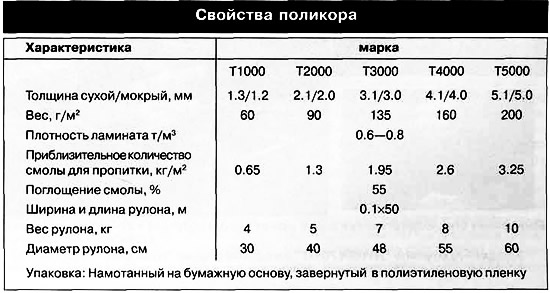
При использовании Т3000, Т4000 и Т5000 необходимо нанести половину требуемого количества смолы на нижнюю сторону поликора, после чего уложить его на ламинат, пропитать оставшимся количеством смолы и прикатать. Обязательно встряхивайте валики и кисти перед началом работы для удаления растворителя, так как он ухудшает качество поликора и тормозит процесс отверждения. Чтобы слои отверждались одновременно, между слоями поликора формуйте слой стеклонаполнителя (для обеспечения правильной массы и отверждения смолы).
В отличие от других стеклонаполнителей, нельзя укладывать поликор внахлест; возможные зазоры между слоями ширинои более 2 мм заполняйте полосками материала, нарезанного ножницами или ножом. Не используйте поликор в качестве последнего слоя; не укладывайте его на поверхность, покрытую гелькоутом.
3. Гелькоут
"Norpol Style Gelcoat" (NSG). В этом году фирма представила на рынок свою новейшую разработку — новый экологически чистый продукт, который произвел переворот в мире производства и использования гелькоута, так как позволяет на 90% снизить эмиссию стирола.
Соблюдение требований защиты окружающей среды становится все более важным фактором в современном производстве композиционных материалов. Ужесточение этих требований продиктовано не только учетом общественного мнения, но и объективными данными, основанными на изучении эмиссии стирола и ее последствий.
"Jotun Polymer" находится в числе лидеров разработки, испытаний и производства высококачественных продуктов с низким выделением стирола (НВС). Уже более 20 лет, полиэфиры Norpol с НВС широко используются во всем мире в самых различных вариантах и модификациях, при производстве высококачественных продуктов, которые являются и химически стойкими и огнеупорными.
Сегодня фирма представляет Norpol Style Gelcoat. Испытания проводились на белом гелькоуте для аэрозольного нанесения. Эти испытания показали, что новый гелькоут выделяет стирол в среднем на уровне 10 г/м2, в то время как стандартный гелькоут НВС выделяет в среднем 11О г/м2. В новом гелькоуте содержится 20% стирола, в то время как в обычном — 36% (это означает 44%-ое снижение содержания стирола).
Гелькоут "НОРПОЛ СТАЙЛ" (ГНС) — новый продукт, внедрение которого особенно важно для производителей, которые серьезно относятся к проблемам охраны окружающей среды.
Испытания ламинатов, полученных с использованием ГНС показали высокую адгезионную прочность — не хуже 175 кг/см2. Но одновременно он обеспечивает значительное сокращение затрат на строительство и монтаж очистных сооружений и вентиляционных систем.
Jotun Polymer — остается ведущим производителем гелькоута в Европе!