Ступицу устанавливают на шаговой горке кормовым торцом вниз с соблюдением заданного ранее положения по высоте относительно базовой поверхности (размер L на рис. в сборнике №98).
Из листа плотной бумаги, картона, прессшпана или другого подобного материала, размер которого немного больше, чем размер лопасти, по разметке на шаговой горке контура лопасти (по рискам входящей и выходящей кромок сечений на шаговых угольниках) вырезают выкройку заготовки лопасти. На выкройку переносят риски, последовательно прижимая заготовку к шаговым угольникам, стараясь перекатывать ее по горке, не сдвигая. Корневую часть выкройки подкраивают по поверхности ступицы.
Информация об изображении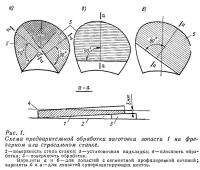
Рис. 1. Схема обработки заготовки лопасти 1 на фрезерном или строгальном станке
Увеличив размер выкройки по всему контуру на 2—4 мм, из листа металла толщиной на 1—2 мм больше, чем толщина корневого сечения лопасти, вырезают заготовки по числу лопастей. Чтобы уменьшить трудоемкость профильной обработки лопастей и облегчить их гибку, вырезанные заготовки необходимо предварительно обработать на фрезерном станке по приведенному эскизу (рис. 1).
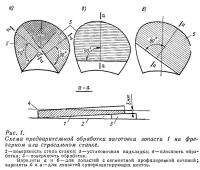
Рис. 1. Схема обработки заготовки лопасти 1 на фрезерном или строгальном станке
Снимая металл с заготовки, припуск по толщинам следует оставлять не менее 2 мм, а кромки заготовки делать не тоньше 3 мм.
Приступая к гибке заготовок и подгонке по шаговой горке нагнетающей поверхности лопастей, надо помнить, что винтовая поверхность из плоского листа может быть образована только при гибке с равномерной вытяжкой металла. Поэтому:
- лучше ударить молотком 10 раз со средней силой, контролируя получаемые деформации, чем перегнуть лопасть одним сильным ударом, при котором вместо плавного изгиба заготовки с дополнительной вытяжкой металла произойдет резкий местный изгиб, сопровождаемый иногда трещинами (правка же лопасти в этом месте очень трудоемка);
- удары молотком следует производить на расстоянии не менее 10 мм от кромки, чтобы обеспечить плавный изгиб в районе центральной части лопасти; удар по кромке обычно приводит лишь к местной деформации.
Как показала практика, лопасть лучше всего гнуть, зажимая заготовку в районе корня в тисках и при помощи 300—500-граммового молотка и 3—4-килограммовой поддержки с узким скругленным концом (рис. 2); в качестве поддержки удобно использовать легкую кувалду. При этом гибка должна проходить между поддержкой и местом удара молотка, а не в месте зажима лопасти в тиски. Чтобы при изгибе заготовки обеспечивалась вытяжка металла, расстояние между поддержкой и центром удара не рекомендуется увеличивать более 30 мм; для предотвращения сильной отдачи поддержку в момент удара следует сильно прижимать к заготовке.
Заготовки толщиной более 10—12 мм целесообразно при гибке разогревать паяльной лампой или газовой горелкой.
Нередко только гибкой подогнать заготовку до плотного прилегания к угольникам шаговой горки не удается. Некоторая подгонка при гибке, а также окончательная обработка нагнетающей поверхности могут выполняться либо опиловкой, либо обдиркой заготовки на наждачном круге (безусловно, лишь в пределах оставленного ранее припуска по толщине лопасти).
Точность подгонки заготовки к шаговой горке проверяют щупом между обработанной поверхностью и рабочей кромкой шаговых угольников; зазоры при этом не должны превышать 0,3 мм. Одновременно заготовку подгоняют и к поверхности ступицы. Зазор в этом случае может быть значительно больше (до 3 мм), так как при сварке он будет заварен.
Припилив заготовку по шаговой горке, на ее поверхность при помощи карандаша или чертилки переносят риски кромок лопасти, а также радиальные сечения (линии прилегания поверхности лопасти к шаговым угольникам). По рискам входящей и выходящей кромок заготовку обрабатывают по контуру, обеспечивая плавность контура лопасти. Линии радиальных сечений по длине разбивают на части в соответствии с чертежом профилировки сечений лопасти, полученные точки фиксируют неглубоким кернением.
Следующий этап — обработка засасывающей поверхности лопасти. Сначала по разметке на нагнетающей поверхности, контролируя толщины штангенциркулем с длинными губками или кронциркулем, обрабатывают отдельные точки на засасывающей поверхности заготовки. Толщины в этих точках выдерживают в соответствии с размерами по чертежу сечений с учетом припуска 0,5—0,8 мм на окончательную обработку лопастей. При двояковыпуклой или выпукло-вогнутой профилировке размер следует снимать с основной линии профиля, соответствующей поверхности шаговой горки, по которой уже была обработана нижняя поверхность заготовки. По полученным точкам аналогично нагнетающей поверхности обрабатывают верхнюю поверхность лопасти, при этом чистота обработки поверхности может быть значительно выше (вплоть до полировки), так как для почти всей поверхности лопастей (кроме района приварки к ступице) она будет окончательной.
Если профилировка сечений двояковыпуклая или выпукло-вогнутая, приступают к окончательной обработке нагнетающей поверхности, делая толщины лопасти соответствующими толщинам профильных сечений.
Обработанные лопасти приваривают к ступице винта. Для качественной сварки в районе утолщенного корневого сечения необходимо произвести разделку кромок, сняв глубокие фаски на лопасти.
Одну из лопастей укладывают на шаговую горку (точно по кромочным рискам) и двумя небольшими прихватками приваривают к ступице. Проверив точность положения лопасти и при необходимости подрихтовав, прихватки делают на противоположной стороне лопасти. Только после этого можно окончательно приварить лопасть, накладывая несколько швов небольшого катета попеременно с двух сторон до наплавки достаточного количества металла для выполнения галтели — скругления в районе стыка лопасти со ступицей.
Приварив одну лопасть, ступицу поворачивают так, чтобы поверхность попасти легла на один из дополнительных шаговых угольников на горке. Фиксируя это положение ступицы, прижимая прихваченную лопасть к угольнику, производят прихватку и приварку следующей лопасти.
После сварки производят обработку галтелей в местах притыкания лопастей к ступице, проверку, при необходимости подгибку лопастей по шаговым угольникам и подрезку лопастей гребного винта по диаметру, обработку кромок, а также расточку посадочных мест.
Чтобы уменьшить до минимума вибрацию и динамические нагрузки на элементы валопровода при работе гребного винта, необходимо провести его статическую балансировку. Точность балансировки винта полностью зависит от качества используемых приспособлений: балансировочного станка — параллельных ножей и фальшвала (рис. 3). Поверхности параллельных ножей и фальшвала должны быть достаточно твердыми, хорошо прошлифованы и не иметь забоин. Материал ножей и вала выбирается достаточно прочным, чтобы исключить прогибы от массы винта. Фальшвал следует изготавливать без боя, а затем точно и плотно устанавливать на посадочные места гребного винта. Длина вала и расстояние между параллелями станка должны позволять гребному винту свободно проворачиваться.
Установив гребной винт с фальшвалом на ножи балансировочного станка так, чтобы ось винта была по возможности перпендикулярна параллелям, при помощи регулировочных винтов необходимо достичь горизонтальности рабочих кромок ножей — гребной винт хотя бы в одном положении не должен скатываться под собственной массой по параллелям. В этом положении элементы гребного винта, расположенные ниже оси, тяжелее, чем те, которые выше, и требуют облегчения за счет равномерного снятия металла. Снимать металл желательно в районе, наиболее удаленном от оси винта, лежащем либо на вертикали, либо симметрично относительно этой линии. Снимая таким образом металл с лопастей, следует добиваться, того, чтобы гребной винт не перекатывался по ножам при любом положении лопастей. (По мере балансировки необходимо производить подрегулировку горизонтальности балансировочного станка, устраняя скатывание винта под действием своей массы.)
Качество окончательной балансировки проверяют простейшим способом: на край одной из горизонтально расположенных лопастей пластелином приклеивают грузик (для винта диаметром до 200 мм — массой 1 г; для 200—300 мм — 2 г; 400—500 мм — 5—6 г). Под его действием винт должен вращаться. Если винт не сдвинулся, следует улучшить качество поверхности фальшвала и ножей балансировочного приспособления и продолжить уравновешивание винта.
Уравновешивая винт, надо следить за тем, чтобы не уменьшить чрезмерно толщину лопастей. Снимать металл следует с засасывающей стороны, обеспечивая плавность поверхности лопасти. Можно балансировать винт, выбирая металл со ступицы опиловкой или сверлением торцевых поверхностей.
После выполнения балансировки винта следует провести окончательную шлифовку и полировку поверхности лопастей.
Для изготовления сварного винта необходимо применять металлы достаточно пластичные, хорошо свариваемые и не дающие подкалки материала в районе сварного шва.
Кроме этого, неоднократно проверенного на практике и рекомендуемого способа многие любители используют другие технологические варианты. Однако имеющийся опыт показывает, что такой способ обеспечивает минимальную трудоемкость изготовления. При достаточном навыке и наличии хорошего инструмента трехлопастной винт из стали диаметром около 250 мм может быть изготовлен за 20—30 ч.