Приспособления для изготовления модели винта и контроля его формы. Ни один из современных способов изготовления гребных винтов не обходится без шаговой горки. Ее собирают на основании — шаговой плите, которая представляет собой стальной диск толщиной 10—15 мм (рис. 1) диаметром около 500 мм (по максимальному диаметру гребных винтов). На плите устанавливают шаговые угольники, согнутые по цилиндрическим поверхностям заданных радиусов. Рабочую поверхность плиты торцуют на токарном станке, на ней через каждые 10 мм по радиусу протачивают кольцевые канавки глубиной 3 мм и шириной 1—2 мм (по толщине материала, из которого делают шаговые угольники). В центре плиты строго перпендикулярно ее поверхности устанавливают вал с центрирующими ступицу гребного винта конусами.
При изготовлении гребных винтов небольшого диаметра шаговые угольники устанавливают в каждой канавке, т. е. с зазором 10 мм. Проверить плотность прилегания лопасти к шаговым угольникам, замерить стрелки вогнутости профиля в ее сечениях в этом случае довольно трудно, поэтому рекомендуем разборную конструкцию шаговой плиты (рис. 2). Ее собирают из дисков диаметром 60, 80, 100 мм и т. д. (в соответствии с радиусами сечений, заданных на чертеже гребного винта), вырезанных из ровного фанерного листа толщиной 10 мм. В дисках строго по центру просверливают отверстия, чтобы их можно было плотно насадить на центрирующий вал. На каждый диск из металлической полосы шириной 8—10 мм делают бандажи, которые стягивают винтом М4, и крепят соответствующие шаговые угольники.
Шаговые угольники образуются при пересечении винтовой поверхности лопасти цилиндром, соосным с осью гребного винта и имеющим радиус данного сечения. Если поверхность цилиндра развернуть на плоскость, получится прямоугольный треугольник, у которого один катет равен шагу винта в данном сечении, а второй — длине окружности основания цилиндра (рис. 3). Острый угол, расположенный против катета, равного шагу винтовой линии, называется шаговым углом. Тангенс этого угла равен соответственно отношению катетов:
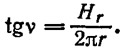
Так как для изготовления гребного винта необходима только часть винтовой поверхности в районе расположения лопасти, размеры шагового угольника можно уменьшить. Для этого необходимо определить высоту угольника в районе образующей (средней) линии лопасти. Сделать это можно по чертежу продольного сечения винта, на котором изображен габарит лопасти, ступица винта и показан наклон образующей. На чертеже наносят с кормового торца ступицы линию, перпендикулярную оси винта и изображающую базовую плоскость поверхности шаговой плиты. В случае применения сборной плиты такие линии проводят для каждого диска. При этом зазор между линией габарита лопасти и шаговой плитой должен составлять не менее 8—10 мм. Высоту шагового угольника — размер А на чертеже — замеряют от базовой плоскости до образующей лопасти (см. рис. 3). Этот размер следует увеличить либо на глубину канавки на шаговой плите, либо на ширину полосы, необходимой для закрепления угольника бандажом при сборной конструкции плиты.
Величина катетов В для построения шаговых углов для каждого радиуса определяется по формуле
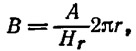
где Нr — шаг лопасти на данном радиусе снимается с графика распределения шага вдоль лопасти.
На гипотенузе шагового угольника размечается положение сечении лопасти: риска средней линии, а также точки входящей и выходящей кромок. Ширина лопасти и положение сечения относительно средней линии снимаются с чертежа спрямленного контура. Для удобства работ по изготовлению лопасти длину шагового угольника следует увеличить с каждой стороны на 10—15 мм. Отклонения при разметке шаговых угольников не должны превышать ±0,3 мм, причем риски наносятся острой чертилкой.
При разметке шаговых угольников корневых сечений, имеющих двояковыпуклый профиль, с рабочей кромки угольника (гипотенузы) необходимо снять полоску металла шириной, равной стрелке выпуклости нагнетающей стороны профиля. Это обеспечит прилегание к шаговому угольнику заготовки лопасти, еще не обработанной по профилю.
В зависимости от технологии изготовления винта необходимо изготовить комплект угольников либо для одной лопасти, либо для всех. Для обеспечения симметрии готового винта для радиуса, близкого к r=0,6R, необходимо изготовить шаговые угольники для всех лопастей.
При установке шаговых угольников для всех лопастей винта с большим дисковым отношением угольники одного радиуса могут перекрывать друг друга. В этом случае в большем вертикальном катете этих угольников надо сделать местный вырез, в который входит меньший катет следующего шагового угольника (рис. 4).
После разметки, вырезки, окончательной обработки и проверки угольники сгибают по цилиндрическим поверхностям заданных радиусов с учетом направления вращения гребного винта.
Для установки угольников на шаговой плите проводят осевую линию лопасти — прямую, проходящую через центр плиты, а на сборной плите из отдельных дисков — осевые линии на каждом диске.
Риску осевой линии на основании шагового угольника точно совмещают с осевой линией на диске, после чего угольник затягивают бандажом. Используя слесарный проверочный угольник, нужно убедиться в том, что цилиндрическая поверхность шагового угольника перпендикулярна плоскости диска (плите). Следует проверить также точность установки угольника по высоте (расстояние А от базовой плоскости плиты до риски, соответствующей образующей на угольнике, должно быть равно размеру на чертеже с точностью ±0,3 мм).
Окружность, для которой изготовлены угольники, надо разделить на равные части по числу лопастей и установить шаговые угольники с соблюдением тех же требований.
Правильность установки шаговых угольников можно проверить, приложив линейку к полученной шаговой горке по рискам образующей, которые все должны лежать на одной прямой. Только на угольниках корневых сечений, высота которых была заранее уменьшена на соответствующую величину стрелки выпуклости нагнетающей стороны, должен получиться зазор. Небольшое несоответствие рисок средней линии лопасти можно компенсировать перестановкой угольников, разворотом дисков сборной плиты. Все торцевые вертикальные кромки угольников должны быть параллельны, а рабочие кромки отстоять друг от друга на одинаковый размер по всей окружности угольников.
Изготовление формы для отливки винта. Литые винты малых размеров изготавливают методам литья по выплавляемым (восковым) моделям1. Для изготовления восковой модели необходимо сделать форму из гипса, цемента или стеклопластика. Для этого нужна «фальшивая» лопасть: форма, выполненная по одной фальшлопасти, получается совершенно симметричной. Проще всего фальшлопасть отформовать из стеклопластика на шаговой горке. Для этого пространство между шаговыми угольниками одной лопасти надо заполнить пенопластом, обрезками дерева и т. п., а затем сверху залить расплавленным парафином или воском. После остывания парафина поверхность горки обрабатывают, выравнивая ее по шаговым угольникам, затем наносят контур лопасти с помощью чертилки, погружая ее острие в парафин на глубину 0,5—0,8 мм.
Фальшлопасть формуется вместе с частью ступицы, для чего следует выточить из дерева фальшивую ступицу и установить ее на горку.
Используя эпоксидный клей, на горку накладывают необходимое число слоев стеклоткани с тем, чтобы получить заготовку примерно на 1—2 мм толще, чем толщина сечения лопасти. После отвердевания стеклопластика лопасть обрабатывают по контуру и профилируют ее сечения.
Для изготовления фальшлопасти можно также использовать оргстекло или фанеру.
Заливка гипсовой формы производится в специальном формовочном ящике (рис. 5), сделанном из оргстекла, текстолита, гетинакса н т. п. Фальшлопасть внутри формовочного ящика должна располагаться с зазором до стенок не менее 10—15 мм. При изготовлении ящика следует обратить особое внимание на точность центрального угла при вершине ящика, определяющего точность положения лопастей относительно оси винта, и на вертикальность стенок, по которым будут стыковаться блоки единой гипсовой формы.
Фальшлопасть, предварительно смазанную разделительным слоем (для этих целей лучше всего использовать касторовое масло, но пригодно и любое другое или солидол), устанавливают в формовочный ящик. Щели, через которые гипс может выливаться, снаружи замазывают пластилином.
Разведенную гипсовую массу заливают в форму. При начале загустевания излишки гипса над верхней поверхностью фалышлопасти аккуратно удаляют с таким расчетом, чтобы в дальнейшем ее можно было свободно вынуть из каждой половинки формы без повреждения ее кромок. При этом целесообразно обвести лопасть по контуру чертилкой, процарапав риску на глубину 0,3—0,5 мм.
После полного отверждения массы поверхности разъема формы и лопасти снова смазывают разделительным слоем и заливают гипсом верхнюю половину, формы. При этом верхнюю поверхность гипса выравнивают по краям формовочного ящика линейкой или ровной планкой.
Когда гипс затвердеет, снимают боковые стенки ящика и верхнюю часть формы, не сдвигая фальшлопасть относительно нижней, ранее залитой половины, и снова подготавливают форму для заливки верхней части следующей формы. Эту операцию повторяют в зависимости от числа лопастей будущего винта.
После отливки последней верхней части разбирают формовочный ящик и снимают нижнюю часть формы, не смещая фальшлопасть относительно этой последней верхней половины. Обычно первая нижняя половина формы имеет поверхность с раковинами, пузырями, недоливом и не используется для составления окончательной формы. Собрав и перевернув формовочный ящик, аналогично отливке верхних половин отливают нижние части формы.
Готовые верхние и нижние части должны с минимальными зазорами собираться в единую форму для отливки единой восковой модели винта, сразу со ступицей и всеми лопастями. В разъеме блоков по контуру лопасти в верхних точках пропиливают канавки — выпоры для сообщения полости формы с атмосферой. Для заливки восковой массы без усадочных раковин над верхним торцом ступицы устанавливают дополнительно форму для прибыли из отрезка трубы диаметром не менее диаметра ступицы винта и высотой 0,3—0,5 длины ступицы. Укрепить эту трубу на собранной форме можно с помощью пластилина.
Перед заливкой воска поверхность формы смазывают разделительным слоем — касторовым или любым другим маслом.
Качественные отливки получаются при заливке воска в тот момент, когда при охлаждении на воздухе полностью расплавленной восковой массы на стенках сосуда появляется тонкий слой загустевшего воска.
Чтобы предотвратить образование раковин и недоливов, заливку воска производят через достаточно широкую трубку, опущенную в отверстие для ступицы Почти до дна формы. По мере заливки и повышения уровня воска в форме трубку приподнимают.
Разбирать форму можно только после полного остывания воска и достаточно осторожно, чтобы не повредить кромки восковой модели.
Мелкие неровности н шероховатость поверхности восковой модели можно удалить, аккуратно протерев поверхность мягкой тряпочкой, смоченной в бензине. Более крупные дефекты можно исправить, закапав эти места расплавленным воском и затем аккуратно зачистив поверхность острым скребком.
Дальнейшую отливку гребного винта из металла по восковой модели выполняют обычными технологическими методами литья по выплавляемым моделям.
Чтобы сохранить модели-«восковки», их надо или вставлять в форму, или проверять перед отливкой их геометрию, вложив в форму. (Описываемый метод пригоден для изготовления формы для отливки «восковок» гребных винтов с дисковым отношением менее 0,8; для винтов с большим дисковым отношением изготовление гипсовой формы значительно усложняется из-за перекрытия лопастей и требует использования совершенно иных приемов формования.)
Технология изготовления форм из стеклопластика описана в сборнике №6 за 1966 г.
Обработку металлической отливки начинают с расточки отверстия в ступице, центруя отливку в патроне токарного станка по наружной поверхности ступицы и симметрии лопастей, а затем выполняют окончательную обработку лопастей, контролируя геометрию винта по шаговой горке и замерами толщин сечений по ординатам подобно обработке лопастей сварного винта, о чем более подробно будет рассказано в дальнейшем.
Изготавливать гребные винты литьем целесообразно при количестве 4—5 шт. Если столько винтов не требуется, лучше остановиться на сварном варианте.
Примечания
1. Технология отливки гребных винтов обычными методами описана в сборнике №6, №16 и №40.