Десятки тысяч любителей в нашей стране являются владельцами дюралевых лодок, так что свойства этого материала хорошо известны. Алюминиевые лодки гораздо дешевле в эксплуатации и не требуют такого ухода, как деревянные, поскольку металл не рассыхается и не гниет. Известные выгоды получают владельцы алюминиевых лодок и благодаря их меньшему весу: выше скорость, меньше расход горючего на пройденный километр, легче(поставить лодку на зимнюю стоянку и транспортировать ее по берегу. Алюминиевый корпус не только легче, но и прочнее, чем деревянный или даже пластмассовый.
Важно . отметить, что помимо высокой прочности алюминиевые сплавы обладают и таким ценным свойством, как пластичность. При растяжении пластинки из алюминиево-магниевого сплава она разрывается после удлинения на 12% (при напряжении 32 кг/мм2). Такая же пластинка из стеклопластика, растягиваемая вдоль основы стеклоткани, разрывается после удлинения всего лишь на 2,5% (при напряжении 22 кг/мм2). Это значит, что, например, в случае одинаково сильного удара на алюминиевом корпусе останется только вмятина, когда на пластмассовом образуется трещина или пробоина.
Все отмеченные свойства, а также сравнительно невысокая стоимость легких алюминиевых сплавов (60— 90 коп. за килограмм) очень важны и для покупателей — владельцев лодок и для промышленности. Но это еще не все. Легкие сплавы имеют и некоторые другие преимущества, не менее ценные с точки зрения судостроителей. Так, высокие физико-механические свойства металла не зависят, как это до сих пор имеет место при постройке пластмассовых корпусов, ни от квалификации рабочих, ни от влажности и температуры воздуха, и не изменяются в течение всего срока службы судна. Постройку лодок из алюминиевых сплавов легче механизировать на всех стадиях процесса — от заготовки деталей до сборки корпуса. В то же время надо подчеркнуть, что организация крупносерийного производства лодок из легких сплавов возможна лишь на предприятиях, хорошо оснащенных сравнительно дорогостоящим и сложным специализированным металлообрабатывающим оборудованием. Выпуск пластмассовых лодок можно наладить с меньшими затратами на технологическое оборудование, но зато и степень механизации труда будет значительно ниже.
С самого начала серийного производства алюминиевых лодок для изготовления корпусов применяются сплавы алюминия с 4—5% меди, т. е. дуралюмины, еще раньше получившие широкое распространение в самолетостроении. Благодаря высокой прочности и твердости дуралюмина обшивка лодки может быть выполнена из очень тонких листов и корпус получается легким. Однако ряд отрицательных свойств дуралюмина делает этот сплав малоперспективным в качестве материала для лодочных корпусов.
Во-первых, медь и алюминий образуют в воде электролитическую пару, и металл интенсивно разрушается межкристаллитной коррозией по всей толщине. Так, известно, что в морской воде тонкая дюралевая обшивка может быть разъедена коррозией насквозь уже через две иавигации. Особенно подвержены разрушению заклепочные соединения.
Во-вторых, дуралюмин относится к так называемым недеформируемым сплавам, которые нельзя штамповать (или, например, отгибать фланцы) в холодном состоянии. Листы дуралюмина приходится перед штамповкой отжигать в селитровых ваннах, а затем готовые детали снова нагревать до 500° С и закаливать в воде. Это значительно осложняет производство, ограничивает выбор обводов корпуса.
Использование дуралюмина Д16 ограничивает и выбор способа соединения деталей: прочность сварных швов (без закалки после сварки) получается недостаточной — вдвое меньше прочности основного металла, поэтому приходится применять клепку.
Всех этих недостатков лишены сплавы алюминия с 2—7% магния, не содержащие меди. Правда, алюминиево-магниевые сплавы обладают примерно в 1,5 раза меньшей прочностью, чем дуралюмины (табл. 1), зато они стойки к коррозии даже в морской воде, достаточно пластичны для холодной штамповки, хорошо свариваются. Показательны проведенные в США испытания коррозионной стойкости образцов листов из сплавов 508З (с содержанием 4,0—4,9% магния) и 5086 (3,5— 4,5% магния) в морской воде в условиях тропиков. Уменьшения прочности металла после 7 лет выдержки в воде обнаружено не было; глубина коррозионных язв на пластине из сплава 5083 после 5 лет не превышала 0,4 мм, а на пластине из сплава 5086 после 6 лет — 0,9 мм. Подобные же сваривающиеся сплавы — АМг, АМг5 и АМг61 получили широкое распространение и в отечественном судостроении при постройке сварных судовых спасательных шлюпок и катеров, при изготовлении надстроек, дымовых труб и мачт пассажирских судов.
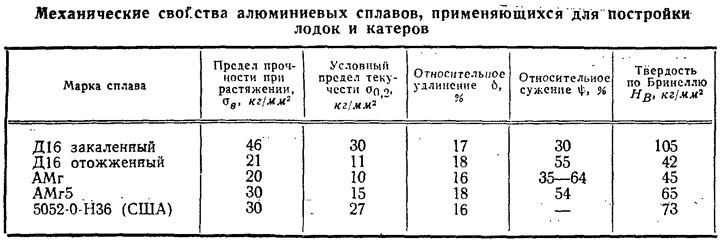
Таблица 1
Характерно, что спрос на лодки из алюминиево-магниевых сплавов в большинстве стран за последние годы значительно повысился. Если в 1955 г. фирмы США выпускали 100000 лодок из таких материалов (33% общего количества построенных в стране малых судов), то в 1966 г. выпуск их увеличился до 235 000 (57% общего количества). Таким образом, в США алюминиевые сплавы уже являются основным материалом для постройки корпусов прогулочных лодок и катеров.
У нас такие прогулочные суда по-прежнему строятся только клепаными и только из дуралюмина. В 1966 г. промышленность СССР дала 15000 дуралюминовых лодок, что составляет лишь около 20% от общего числа лодок, поступивших в продажу. В связи с тем что в ближайшие годы планируется увеличить производство лодок для продажи населению, по крайней мере, в четыре раза, уже в 1967 г. алюминиевые лодки стали продукцией «ширпотреба» ряда мощных предприятий и начата разработка новых моделей (часть из них представлена в этом выпуске сборника). Правда, руководители некоторых заводов избрали наиболее легкий и проторенный путь: они включили в план постройку дуралюминовой «Казанки», выпускаемой нашей промышленностью в течение почти двадцати лет.
Надо прямо сказать, что «Казанка» безнадежно отстала от современных мировых стандартов как по эксплуатационным качествам, так и по конструкции. То, что она находит сбыт, можно объяснить лишь отсутствием в продаже лодок других моделей. В самом деле, взгляните на теоретический чертеж «Казанки». Это по существу узкий ящик, заостренный в носу. Ширина лодки всего 1,2 м, в то время как аналогичные современные мотолодки имеют ширину 1,6—1,7 м. Остойчивость «Казанки» при полной нагрузке (четыре человека плюс снаряжение для похода) недостаточна даже с подвесным мотором «Москва», а при установке «Вихря» избежать переворачивания может только опытный водитель. Не приходится говорить о способности этой лодки идти на волнении — кокпит сильно забрызгивается, днище хлопает о воду. И при всем этом завод-изготовитель допускает эксплуатацию «Казанки» с мотором мощностью до 25 л. с. с нагрузкой 400 кг и на волне высотой до 1,2 м!
Не обеспечена безопасность экипажа в случае опрокидывания или заливания лодки. Воздушные отсеки расположены так, что корма с тяжелым мотором полностью уходит под воду. Вряд ли лодка способна в таких случаях оставаться на плаву с разрешаемым заводом грузом (400 кг). Недостаточно жесткий транец при работе мотора вибрирует, как мембрана. Видимо, из-за этого на «Казанках» с «Вихрем» часто обнаруживают течь из-под заклепок. Наружная килевая накладка быстро изнашивается при вытаскивании лодки на берег.
Неудачна и сложна в производстве конструкция лодки с большим количеством деталей набора (шпангоутов и стрингеров) и массой заклепок, рассчитанная на применение большой доли ручного труда при сборке и клепке. Это является причиной высокой себестоимости лодки (в некоторых случаях производство «Казанок» даже убыточно).
К сожалению, конструкция новых моделей лодок («Прогресс», «МКМ», «Лотос») во многом копирует конструкцию все той же «Казанки». По-прежнему постройка этих лодок планируется на полукустарных участках «ширпотреба», в то время когда есть все возможности для организации их производства индустриальными методами на конвейерах специализированных цехов с высоким уровнем механизации труда.
Как уже отмечалось, до сих пор не используются конструкционные возможности новых сваривающихся сплавов. Необходимо заменить дуралюмин алюминиево-магниевыми сплавами. При сохранении прежнего типа конструкции толщину обшивки, например из АМг, пришлось бы увеличить на 25—30% для компенсации меньшей прочности материала (табл. 2). Однако пластичные свойства сплава и применение сварки вместо клепки позволяют осуществить такую замену без заметного увеличения веса.
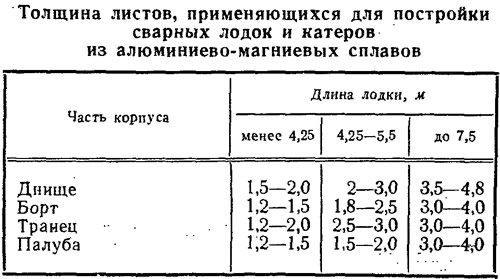
Таблица 2
Так, вместо приклепываемых продольных ребер жесткости (стрингеров) из угольников в листах обшивки могут быть прокатаны глубокие зиги — гофры. Может быть изготовлена и обшивка типа клинкер (кромка на кромку). «Кромки» поясьев такой обшивки образуются при прокатывании листа в вальцах или на зиг-машине; высота «кромок» невелика — всего А—5 толщин листа, но это равноценно по жесткости увеличению толщины листа на 10—15%. При наличии достаточно мощного пресса (200—300 т) можно сразу отштамповать цельную обшивку небольшой лодки со всеми брызгоотбой-никами и зигами.
В ряде случаев целесообразно избрать более выгодную в технологическом отношении круглоскулую форму корпуса. Для гибки половин обшивки такого корпуса (с разъемом по ДП) могут быть использованы имеющиеся на наших заводах обтяжные прессы. В этом случае матрица не нужна, достаточно одного пуансона. На таком прессе могут быть также изогнуты привальные брусья, кили и другие детали. На нем удобно гнуть борта и днища и остроскулых лодок. Надо отметить, что в зарубежной практике широкое использование обтяжных прессов (наряду с применением сварки и прессованных профилей) является одной из характерных тенденций лодочного корпусостроения.
Таким образом может быть уменьшено количество элементов набора, соединений и сложных узлов, изготовление и сборка которых удорожают постройку. Упрощается и поперечный набор, детали которого можно штамповать и гнуть в холодном состоянии из листа. Штампованный профиль более жесткий и прочный, чем стандартный угольник того же веса, поэтому штампованные шпангоуты могут быть установлены реже.
Прочность и жесткость обшивки легких гребных лодок и каноэ обычно обеспечивается за счет большой кривизны обводов (обшивка работает как скорлупа яйца), поэтому набор на таких малых судах можно ограничить килем, привальными брусьями, несколькими флорами и банками или распорками.
Большие возможности открывает применение специальных прессованных профилей для соединения листов обшивки по килю, скуле, планширю. Из алюминиевых сплавов может быть изготовлен профиль практически любого сечения вплоть до панели. с уже готовыми ребрами таврового профиля. Наиболее употребительные в иностранном катеростроении сечения прессованных профилей показаны на рисунках. Их использование значительно упрощает конструкцию узлов и соединений, удешевляет постройку корпуса, повышает его прочность и жесткость, надежно защищает от износа. В сварных конструкциях такие элементы являются технологически необходимыми.
И, наконец, при переходе на алюминиево-магниевые сплавы клепка может быть полностью заменена более производительной сваркой. Так, большинство ведущих катеростроительных фирм США уже перешло на постройку цельносварных корпусов; по их свидетельству применение сварки экономичнее клепки на 25%. Электродуговая сварка сплавов типа АМг в среде инертных газов (обычно аргона) освоена и на отечественных предприятиях, которые имеют современное оборудование не только для ручной, но и для полуавтоматической и автоматической сварки.
Основной проблемой, возникающей при сварке корпусов из листов толщиной 1,5—2,5 мм, является борьба со сварочными деформациями, т. е. выпучиванием, короблением листов вследствие их интенсивного местного нагрева сварочной дугой. Качественный корпус из легкого сплава сварить значительно труднее, чем стальной, так как коэффициент линейного расширения алюминия при нагревании в два раза выше, а модуль нормальной упругости в три раза ниже, чем у стали. Поэтому для сборки и сварки алюминиевых лодок необходимо применять специальные стапель-кондукторы, обеспечивающие точность обводов готового корпуса.
В качестве примера на снимке показан кондуктор для сварки мотолодки длиной 4,3 м. Он состоит из жестких поперечных лекал, установленных на прочной раме вверх килем. В специальные гнезда в этих лекалах при сборке укладываются прессованные профили привальных брусьев, скуловых стрингеров и киля; затем накладываются и плотно прижимаются к набору пневматическими прижимами листы обшивки. Для контроля поджатия листов и профилей к лекалам применена специальная система контрольных лампочек на пульте управления. Сварка основных продольных швов осуществляется автоматически; сварочная головка закреплена на портале и имеет простейшую следящую систему, ведущую дугу точно по соединению. Сравнительно высокая скорость сварки (1—1,5 м/мин) способствует уменьшению выделяемого тепла. Вдоль сварных швов в кондукторе закреплены стальные трубы, в которых циркулирует охлаждающая вода. Благодаря этому выделяемое при сварке тепло интенсивно поглощается, что наряду с жестким закреплением свариваемых элементов препятствует короблению конструкции. Важную роль в поглощении тепла играют также массивность и жесткость прессованных профилей, на которых завариваются швы. Рама кондуктора смонтирована на цапфах так, что корпус может быть повернут в наиболее удобное для сборки и сварки положение. Вся установка обслуживается двумя рабочими — судосборщиком и сварщиком.
Таковы в общих чертах основные направления совершенствования конструкции и технологии постройки алюминиевых лодок. Возможно, в некоторых случаях будет трудно сразу перейти на сварку. Но, как показывает опыт, и клепаную конструкцию можно значительно упростить и удешевить за счет сокращения количества деталей набора и применения прессованных профилей сложного сечения.
Нельзя не сказать несколько слов о порядке разработки новых моделей лодок; впрочем, беда как раз в том, что какого-либо установленного порядка и единых требований к проектам лодок народного потребления нет. Любой завод, приступающий к производству этого вида «ширпотреба», волен делать все по своему усмотрению. В лучшем случае, разработка чертежей попадает в руки любителей, имеющих лишь общее знакомство с гидромеханикой и конструкцией судна. Нам кажется, что отработка типовых проектов лодок должна вестись в опытовых бассейнах и специализированных конструкторских бюро и лишь после этого документация должна передаваться на заводы, какому бы ведомству они не принадлежали. Целесообразность такого пути очевидна, если учесть, что общее количество выпускаемых лодок уже измеряется десятками тысяч.