Прежде всего, это высокая проходимость водометных судов, делающая доступными многие мелководные реки, упрощающая подход к необорудованному берегу и стоянку лодки на воде. Ротор водометного движителя лучше защищен от повреждений при наезде на подводные препятствия или плавающие предметы, в результате чего гребные винты чаще всего лишаются лопастей. Водометный движитель, снабженный гидрореверсивным устройством, гораздо проще в изготовлении своими силами, чем угловая поворотно-откидная колонка или реверс-редуктор. С водометом могут быть спарены мощные и экономичные двигатели, «головки» подвесных моторов, двигатели от мотоциклов.
Основные данные катера «Мурена»
Длина наибольшая, м | 4,00 |
Ширина наибольшая, м | 1,65 |
Ширина по скуле у транца, м | 1,30 |
Высота борта на миделе, м | 0,67 |
Масса порожнем, кг | 160 |
Мощность двигателя, л. с. | 30—70 |
Скорость максимальная при двигателе от ПМ « Вихрь-30», км/ч | 40 |
Нужно, однако, сразу же оговориться, что каких-либо преимуществ в скорости, по сравнению с винтовыми катерами, водомет не имеет. Наоборот, дополнительное сопротивление воды, омывающей водозаборник, подъем ее (пусть даже на небольшую высоту) для выпуска в надводной части корпуса катера обусловливают некоторое снижение скорости водометных судов. Это снижение может быть весьма значительным при небрежном изготовлении движителя и применении его на не подходящих для этой цепи судах. Опыт показывает, что лучшие результаты можно получить при использовании водомета на легких глиссирующих лодках, оснащенных достаточно мощным двигателем.
Эти соображения и были учтены при подготовке очередного проекта лодки для самостоятельной постройки. Предлагаемый вариант предусматривает установку на «Мурену» двигателя от 30-сильного «Вихря» со штатным редуктором, но без дейдвудной части, подвески и капота. Нужно будет изготовить легкий фундамент, опирающийся на продольные балки набора корпуса, смонтировать системы охлаждения и выпуска и, конечно, изготовить водометный движитель.
Вместо двигателя ПМ можно установить любой другой, близкий по основным характеристикам — мощности, массе, частоте вращения и габаритам. Двигатель от автомобиля «Москвич» для предлагаемой лодки будет немного великоват; в этом случае корпус лучше удлинить до 4,75—5 м.
Выполнены пожелания многих читателей «КиЯ»: конструкция корпуса предусматривает его постройку из стеклопластика либо композитной конструкции — из пластика на деревянном наборе. Последний способ удобен для индивидуального строительства, так как не требуется изготовлять довольно трудоемкую оснастку — пуансон и матрицы, которые затем выбрасываются.
Не исключено изготовление корпуса и целиком деревянной конструкции. В этом случае отсыпаем читателя к третьему изданию книги «15 проектов судов для любительской постройки» («Судостроение», 1985 г.), в которой достаточно подробно описываются приемы основных работ и по которой можно подобрать сечения всех связей набора, пользуясь близким по размерениям проектом. Для облегчения обшивки бортов в носовой части, имеющих вогнутость, можно использовать полосы фанеры шириной 150— 200 мм, укладывая их по диагонали под 45° к привальному брусу обязательно в два слоя. Затем обшивка обклеивается двумя слоями стеклоткани на эпоксидном связующем.
Несколько слов об обводах лодки. Они типичны для современных глиссирующих судов, эксплуатируемых на реках при высоте волны до 0,75 м. Благодаря умеренной килеватости днища (17° у транца) перегрузки при ходе на волнении невелики. Широкие скуловые брызгоотбойники и продольные реданы позволяют несколько повысить гидродинамическое качество и уменьшить количество брызг, вырывающихся из под днища. Высокий надводный борт и большая ширина корпуса по палубе обеспечивают безопасность плавания на волне указанной высоты и удобство для размещения в сравнительно маленькой лодке четырех человек.
Если принимается композитная конструкция, то начинать изготовление корпуса следует с заготовки шпангоутов и элементов продольного набора. Главная роль облегченных шпангоутов — придать корпусу его форму. Их можно вырезать из 8—12-миллиметровой фанеры, склеивая отдельные полосы на ус в районе скул. Можно применить и более тонкую фанеру, используя ее для фанеровки с обеих сторон шпангоутов собранных из 7—8-миллиметровых дощечек. Реже любители собирают шпангоуты из твердого пенопласта толщиной до 30 мм, оклеивая их после формования обшивки несколькими слоями стеклопластика.
Шпангоуты необходимо делать до полной высоты бортов вместе с участками палубы или бимсами. На плазе следует сразу же разметить шергень-линию, пользуясь которой к шпангоутам крепят временные планки. Затем шпангоуты и выклеенный заранее по шаблону из двух реек форштевень с килем устанавливают на стапель, состоящий из двух параллельных досок. Корпус будет строиться в положении вверх килем, как и лодки деревянной конструкции.
Некоторую трудность может вызвать изготовление выпуклого транца. Его форма задается двумя шельфами 3 и 29, задняя кромка которых обрабатывается по радиусу. К ним крепится листовой оформитель — стеклотекстолит или тонкая фанера, затем бруски для оформления кромок днища и бортов. Выпуклый транец улучшает внешний вид катера но, если этим поступиться, можно сделать его плоским.
Когда шпангоуты, транец и киль форштевнем установлены и выровнены на стапеле, в шпангоуты врезают рейки привальных брусьев и скуловых стрингеров. Можно заметить, что их поперечное сечение значительно меньше, чем у лодок деревянной конструкции, — так же как и шпангоуты, продольные рейки служат только для оформления обводов корпуса Необходимая ширина скулового брызгоотбойника получается подклеиванием к стрингеру коротких реек или кусков пенопласта между шпангоутами. На этой же стадии на днище между шпангоутами вставляют пенопластовые оформители продольных балок фундамента двигателя, которые впоследствии оклеивают стеклотканью. Расстояние между балками должно быть согласовано с подмоторной рамой или кронштейнами для крепления двигателя.
Прикладывая к рейкам выставленного набора кусок фанеры, с их кромок снимают малку, затем укрывают набор листами стеклотекстолита толщиной 1,5—2 мм Если достать этот материал не удастся, то листы можно изготовить самостоятельно, используя стеклоткань и связующее, заготовленные для формования корпуса. Процесс описан Л. Нефедовым в «КиЯ» №122.
Листы нужных размеров выклеиваются на стопе, обязательно установленном на открытом воздухе. На столе расстилается калька либо целлофан или полиэтилен служащие разделительным споем. На него накладывают 3—5 слоев стеклоткани, на которые равномерно наносится эпоксидное связующее с введенным в него пластификатором и отвердителем и пакет проглаживается разогретым утюгом. Благодаря тому, что вязкость разогретой смолы снижается, связующее хорошо пропитывает все слои стеклоткани. На те места, где связующего оказалось недостаточно, можно нанести дополнительную его порцию и вновь прогладить утюгом. Через 20—30 минут наступает процесс частичной полимеризации, при котором лист пластика приобретает определенную жесткость, но его еще можно резать сапожным ножом и пробивать сквозь него мелкие сапожные гвозди.
При проглаживании утюг необходимо периодически очищать от налипшей на него смолы при помощи острого ножа, а также следить за тем, чтобы утюг не задерживался на одном месте. Нагретый участок может прочно приклеиться к утюгу и заготовка пластика окажется испорченной.
С места корпуса, которое предполагается закрыть листом пластика, снимается шаблон из картона или плотной бумаги, обрезается по кон туру и накладывается на заготовку для разметки. Кромки деталей набора, которые будут прилегать к листу, смазываются связующим, затем заготовка ставится на место и крепится к шпангоутам и рейкам продольного набора мелкими гвоздиками. Если лист пластика провисает под собственным весом, следует продолжить процесс полимеризации связующего — повесить лист на солнце либо использовать для подогрева рефлекторы. При этом нужно проверять, чтобы заготовка не стала настолько жесткой, чтобы пластик нельзя было пробить гвоздем или изогнуть лист по обводам корпуса. Если применяется готовый стеклотекстолит, в нем придется просверлить отверстия для гвоздей.
Таким образом закрывается вся поверхность корпуса. Стыки и пазы отдельных листов желательно выполнять на кромках набора. Все неровности обшивки шпаклюют эпоксидной шпаклевкой, стыки и пазы проклеивают лентами стеклоткани в 2—3 слоя.
После выдержки в течение двух-трех суток пластик приобретает достаточную твердость, чтобы ошкурить его поверхность и приступить к обклейке всего корпуса дополнительными слоями стеклоткани до нужной толщины (на днище 4—4,5 мм, на бортах 3—3,5 мм). При укладке последнего слоя стеклоткани в связующее можно добавить красящий пигмент либо окрасить лодку после постройки пентафталевыми эмалями.
Пользуясь этой технологией, можно заранее изготовить трехслойную переборку шп. 5 с пенопластовым заполнителем между наружными слоями стеклопластика, а также продольные выгородки в моторном отсеке, отделяющие топливные баки и аккумуляторную батарею от двигателя.
Особого внимания требует формование продольных реданов. Лучше всего, обклеив корпус двумя-тремя слоями стеклоткани, наклеить на днище заготовки реданов из твердого пенопласта (в крайнем случае из дерева) и обклеить их в 2—3 слоя лентами стеклоткани так, чтобы края лент переходили на днище на 25—40 мм. Последующие слои стеклоткани на днище укладывать в виде узких полос между реданами.
Киль и форштевень, места перехода транца в днище и борта рекомендуется усилить дополнительными слоями ткани.
После освобождения корпуса от стапеля, его переворачивают и приступают к оформлению палубы. Делается это путем вклеивания брусков из пенопласта между шпангоутами. После полимеризации клея выступающие за кромки шпангоутов части пенопласта срезают, обрабатывают пенопласт рубанком или «теркой» (лист жести с пробитыми в нем гвоздем отверстиями с заусенцами), затем грубой шкуркой. В носу и корме в бимсы врезают рейки, которые будут поддерживать листы стеклотекстолита при наклеивании на них слоев стеклоткани.
Накрыв кормовую и носовую части палубы стеклотекстолитом, в корме оформляют из деревянных реек вырез люка. На кромки этих реек, смазанных разделительным слоем (например, вазелином или мастикой для пола), загибаются края стеклоткани, образуя комингс выреза люка; после отверждения пластика рейки удаляют, а в стеклотекстолите делают соответствующий вырез. В носу на палубу наклеивают пенопласт для образования выступа для крепления ветрового стекла. Затем на палубу наформовывают дополнительные слои стеклоткани (на пенопластовые оформители бортовых ее участков достаточно наклеить 2—3 слоя).
Несколько слов о материалах для изготовления корпуса «Мурены». Прочный и водонепроницаемый корпус получается, если использовать стеклоткани сатинового переплетения марок Т11-ГВС-9, АСТТ (б) С2. При собственной толщине этих тканей 0,25—0,3 мм один слой стеклопластика в обшивке дает толщину 0,4—0,5 мм, так что на днище нужно уложить (с учетом толщины оформителя из стеклотекстолита) 8—10 слоев ткани, на борта — 6—7 слоев. Всего на изготовление корпуса «Мурены» необходимо 130 м стеклоткани, которая выпускается шириной 0,9 м.
Для наружного слоя и приформовки различных деталей рекомендуется более тонкая стеклосетка СЭ-01 полотняного переплетения. Она скрадывает грубую текстуру стеклоткани, хорошо выравнивает поверхность, плотно облегает сопряжения по небольшим радиусам и хорошо удерживает декоративный слой смолы.
Важно выдержать условие, чтобы вес связующего, используемого для формования слоя, был равен весу армирующей ее стеклоткани; лучше, если отклонения в ту или иную сторону не превышают 5%.
Работы по формованию корпуса нужно вести в хорошо вентилируемом помещении или на открытом воздухе. В последнем случае важно выбрать сухую и теплую 17—25 °С погоду. Работать нужно в резиновых перчатках, тщательно смывая с кожи капли связующего. При обклейке корпус: сначала на его поверхность кистью или шпателем наносят слой связующего, затем укладывают стеклоткань и тщательно разглаживают ее, добиваясь хорошей пропитки и исчезновения складок и воздушных пузырей. Если поверхность укладывают несколькими полотнищами ткани, их кромки должны перекрывать друг друга на 20—40 мм. При обклейке палубы кромка полотнища должна заходить на верхнюю кромку наружной обшивки на 25 мм.
Рекомендации по изготовлению пуансона, матриц и формованию безнаборного корпуса можно найти в статье о постройке мини-яхты «Калан» в «КиЯ» №50. Полезна также книга П. П. Каткова, В. В. Кушелева «Технология пластмассового судостроения», Л-д, 1986 г. «Судостроение».
Водометный движитель
Па катере предусмотрена установка одноступенчатого водометного движителя. Основными его деталями являются: водозаборник с защитной решеткой на входе и фланцем для крепления движителя к транцу катера; четырехлопастной ротор, имеющий дисковое отношение A/Ad=0,8, диаметр 189 и шаг 190 мм; сопло с вмонтированным в него спрямляющим аппаратом; реверсивно-рулевое устройство и гребной вал с подшипниками и дейдвудным уплотнением.
Водозаборник представляет собой патрубок довольно сложной конфигурации. Его конец, примыкающий к днищу, имеет прямоугольное сечение, которое постепенно переходит в цилиндр в месте расположения ротора. Если корпус катера строится из стеклопластика, имеет смысл изготовить водозаборник также из пластмассы и приформовать его нижнюю кромку непосредственно к днищу корпуса. Для этого не потребуется металлический крепеж.
Ротор вращается в статоре — стальном кольце, благодаря чему обеспечивается необходимая износостойкость внутренней поверхности водомета и точность его сборки. С изготовления этого кольца и привариваемого к нему фланца и следует начать работу. Для металлических деталей движителя желательно использовать нержавеющую сталь; следует по возможности избегать применения разнородных металлов для предотвращения коррозии.
Окончательную обработку внутренней поверхности кольца по диаметру 190 мм и проточку центрирующего пояска для сборки с направляющим аппаратом нужно выполнить после приварки фланца. На поверхности обечайки, к которой будет приформовываться стеклопластиковый водозаборник, необходимо нарезать канавки глубиной около миллиметра для более надежного сцепления металла с пластиком. Внутреннюю поверхность кольца, омываемую водой, желательно отполировать для уменьшения потерь на трение.
Для формования водозаборника необходимо изготовить форму — «болван», которая в точности копирует внутреннюю поверхность патрубка и обеспечивает сопряжение с деталями, замоноличиваемыми а пластик. Теоретический чертеж водозаборника приведен в предыдущем номере. После отверждения стеклопластика болван приходится удалять из водозаборника, что обязательно нужно учитывать. Проще всего сделать его из небольших кусков пенопласта, соединяя их между собой «точечной» склейкой эпоксидным связующим.
На тонкой пенопластовой плите размером 600X250 мм нужно вычертить контур водозаборника в ДП. Обрезав плиту по этому контуру, с боков к ней приклеивают две части основания, обработанных по контуру днищевого отверстия. Затем к вертикальной плите приклеивают две половники диска диаметром 190 мм, оформляющего цилиндрический конец патрубка, иа который можно насадить кольцо статора. Остается заполнить пространство между этими плитами кусками пенопласта и обработать их, контролируя поверхность при помощи шаблонов поперечных сечений, вырезанных из фанеры. Окончательную обработку выполняют шкуркой, затем поверхность шпаклюют, вновь обрабатывают шкуркой и окрашивают. По контуру входного отверстия водозаборник должен иметь фланец шириной 20—25 мм для приформовки к днищу, поэтому болван нужно поставить на основание из толстой фанеры.
Далее нужно подготовить закладные части — корпус смотрового лючка, корпус дейдвудного подшипника. воздушный штуцер и планки для крепления решетки. Требуемая точность монтажа линии вала обеспечивается при помощи «фальшивого» вала и центрирующего диска, совмещаемого с наружным отверстием статора. Пропустив вал через отверстие, просверленное в болване, на его внутренний конец надевают корпус дейдвудного подшипника или, в случае, если упорный подшипник вмонтирован а редуктор двигателя, патрубок для крепления сальника. Второй вариант предпочтительнее, так как отпадает необходимость в точной центровке линии вала в пределах водометного движителя. Затянув гайки на концах фальшвала, фиксируют центрующий диск и корпус подшипника на болване.
У входной части водозаборника к болвану крепят полоски резины толщиной 4 мм для того чтобы на внутренней поверхности водозаборника получились углубление под пластинки, к которым привинчивают защитную решет-ку.
Поверхность болвана покрывают разделительным слоем (разведенный в скипидаре воск, мастика для натирания паркетных полов, вазелин и т. п.), который должен обеспечить легкое отделение болвана от стеклопластика после его отверждения. Поверхности металлических деталей, которые должны надежно склеиться с пластиком, зачищают и тщательно обезжиривают ацетоном либо другим растворителем. Затем наносят декоративный слой, который предохранит поверхность стеклопластика от износа, позволит получить гладкую глянцевую поверхность водовода. Декоративный слой приготавливают из эпоксидного связующего с введением в него 10% двуокиси титана, окиси хрома или алюминиевой пудры. После желатинизации пигментированного слоя можно приступать к выклеиванию водозаборника.
Стеклоткань нужно раскроить на куски и полосы с таким расчетом, чтобы слои ее плотно ложились на поверхность болвана без морщин и пузырьков воздуха. Нанеся слой связующего, накладывают слой стеклоткани и тщательно приглаживают ее к поверхности, следя, чтобы связующее равномерно, без пропусков, проступило сквозь ткань. Общая толщина стеклопластика должна составлять 6—8 мм. Наклеив несколько слоев ткани, устанавливают на свои места корпус смотрового лючка, воздушный штуцер и закладные металлические планки с резьбовыми отверстиями для крепления защитной решетки, затем продолжают формование.
Есть и другой вариант установки решетки: после снятия водозаборника с болвана под концы продольных полос решетки в стеклопластике пропиливают вертикальные пазы, вставляют полосы и временно закрепляют их при помощи клинышков, затем заклеивают пазы эпоксидным клеем со стекловолокном. Крепление концов получается более надежным, если у концов в полосах просверлить отверстия.
Лучше всего завершить формование водозаборника за одни прием и выдержать его на болване в течение двух суток, после чего можно вынимать из него пенопластовый болван. Это можно делать сразу с двух сторон патрубка.
Болван можно изготовить из гипса или дерева, применить для облегчения обработки наружной поверхности воск или пластилин. При изготовлении по одному болвану нескольких водозаборников удобен деревянный болван разъемной конструкции, описанный в 3-ем издании книги «15 проектов судов для любительской постройки».
Иногда предпочтительнее изготовить водозаборник из тонколистового (2—3 мм) металла. И в этом случае тоже необходим болван, по которому делают предварительную разметку отдельных частей водозаборника, имеющих сравнительно простую погибь. Для каждой части вырезают шаблон из картона или тонкой жести, который используется для разметки на металле. Заготовки подвергают выколотке — придают им нужную форму, нанося удары молотком со скругленной ударной частью по внутренней поверхности заготовки, положенной на торец березовой чурки. Периодически заготовки прикладывают к болвану для контроля их формы.
По окончании выколотки заготовки подгоняют друг к другу по кромкам и, уложив на болване, прихватывают сваркой. Окончательная сварка выполняется после прихватки днищевого фланца и цилиндрического кольца статора. Все швы заваривают снаружи, места сварки тщательно зачищают; внутреннюю поверхность водозаборника желательно отполировать.
Устанавливать и приваривать корпус дейдвудного подшипника нужно при помощи такого же кондуктора с фальшвалом, как и в случае стеклопластикового водозаборника.
Сопло и спрямляющий аппарат. Для изготовления сопла нужно по размерам, приведенным иа чертеже, выточить на токарном станке из твердого дереаа или металла болваи и по нему выколотить или выдавить обечайку из нержавеющей стали толщиной 2—3 мм. Для облегчения этой работы заготовку сопла можно выкроить в виде трех — шести лепестков с припуском по кромкам для последующей подгонки; каждый йз лепестков выколачивается до плотного прилегания к поверхности болвана. Уложив подогнанные друг к другу лепестки на болван, их стягивают хомутами из мягкой проволоки, затем надевают на бопааи фланец и прихватывают его к лепесткам. Окончательную сварку швов ведут небольшими участками на диаметрально противоположных сторонах сопла, чтобы избежать коробления.
Заготовки лопаток спрямляющего аппарата изгибают и обрабатывают, контролируя форму поперечного сечения по шаблону. Вытачивают ступицу, подгоняют и приваривают к ней концы лопаток. Для обеспечения точности сборки лучше всего изготовить сборочный кондуктор, в котором фиксируются лопатки, ступица и фланец крепления сопла к водозаборнику. После сварки лопаток со ступицей их внешние концы протачивают по продольному профилю сопла, затем все детали крепят в кондукторе. Здесь к торцу обечайки приваривают фланец, заваривают швы по концам лопаток. Затем производится окончательная проточка посадочного углубления во фланце и расточка втулки под резино-металлический подшипник. В обечайку вваривается штуцер для забора воды в систему охлаждения двигателя.
Все поверхности спрямляющего аппарата, омываемые водой, зачищают от наплывов сварки, мелкие раковины шпаклюют эпоксидной шпаклевкой, все попируют.
Ротор. Четырехлопастной ротор может быть изготовлен литым (из латуни, алюминиевого сплава) либо сварной конструкции (из стали).
Для обработки лопастей необходимо изготовить шаговую горку, состоящую из основания-плиты — диска с проточенными в ней кольцевыми канавками для установки шаговых угольников, самих угольников и коитршаблонов для контроля поперечного сечения лопасти на заданных чертежом радиусах. Шаговые угольники и контршаблоны вырезают из 1,5—2-миллиметровых листов металла и изгибают по соответствующим радиусам.
Ротор водомета — правого вращения. Это значит, что правая кромка лопасти должна быть выше левой, если смотреть на лопасть с ее внешнего конца. Заранее выточенная ступица ротора устанавливается на плиту задним торцом вниз и центруется при помощи короткого валика.
Общая последовательность работ по изготовлению сварного гребного винта или ротора описывается в упоминавшейся книге «15 проектов». Заметим, что винтовая поверхность нагнетающей стороны попасти может быть получена из плоской заготовки только при гибке с равномерной вытяжкой металла. Лопасть изгибают, зажимая корневое сечение заготовки в тисках и нанося по ней удары молотком. С обратной стороны лопасть нужно поддерживать легкой кувалдой. При этом лопасть должна гнуться между поддержкой и местом нанесения удара, а не в корне. Поверхность лопасти контролируют, прикладывая заготовку к шаговой горке; зазор между лопастью и кромкой угольника не должен превышать 0,3 мм. Окончательную доводку осуществляют драчевой пилой.
Выпуклую (засасывающую) сторону обрабатывают, пользуясь контршаблонами для данных радиусов. Поперечные сечения лопастей — сегментного профиля, т. е. представляют собой часть круга, ограниченную хордой, совпадающей с нагнетающей стороной. Имея три заданные точки профиля — толщину и ширину сечения, несложно найти величину радиуса для построения спинки профиля. Можно также воспользоваться ординатами профиля, приведенными, например, в «Справочнике по катерам, лодкам и моторам» (1982, «Судостроение»). Затем лопасть прихватывают электросваркой к ступице, рихтуют и окончательно приваривают короткими участками попеременно с обеих сторон лопасти.
После сварки всех лопастей проверяют плотность их прилегания к шаговым угольникам, при необходимости подгибают, обрезают ротор по диаметру, обрабатывают сварные швы и растачивают отверстие в ступице под гребной вал. Готовый ротор нужно подвергнуть статической балансировке на станке с параллельными и горизонтальными ножами. Отбалансированный ротор не должен самопроизвольно поворачиваться на ножах. Металл со стороны более тяжелой лопасти, которая оказывается внизу, снимается с внутренней стороны ступицы. Разумеется, лопасти и наружную поверхность ступицы необходимо полировать.
Валопровод. Показанный на чертеже корпус дейдвудного подшипника рассчитан на установку радиально-упорного шарикоподшипника № 46205. Если такого подшипника не достать, следует откорректировать размеры под имеющийся в наличии, способный выдержать осевую нагрузку до 200 кгс при частоте вращения около 4000 об/мин. Можно выполнить этот узел по типу «вихревского» редуктора — с упорным подшипником № 8106 и игольчатым 2.109-000 или встроить упорный узел гребного вала в редуктор.
Резино-металлический подшипник можно изготовить самостоятельно, воспользовавшись помощью авторемонтной мастерской. Выточив из бронзы или латуни втулку подшипника, ее заполняют мелко нарезанными кусочками сырой маслобензостойкой резины, применяемой для ремонта автомобильных шин. Втулку вставляют со скользящей посадкой в стальной стакан и уплотняют резину при помощи плунжера, осаживаемого любым прессом. Затем стакан с втулкой помещают на 2,5 часа в варочную плиту. После остывания в резине сверлят отверстие диаметром на 2 мм меньше шейки вала и прорезают вдоль него четыре канавки треугольного сечения для подтока воды, которая в данном случае служит смазкой.
Реверсивно-рулевое устройство ( РРУ)
Управление катером по курсу и задний ход обеспечиваются за счет изменения направления струи воды, истекающей из сопла водометного движителя. С этой целью близ торца сопла на его цилиндрической насадке закреплена поворотная насадка 9, которая имеет возможность поворачиваться относительно вертикальной оси на 35° на оба борта. На этой насадке шарнирно закреплена заслонка реверса 8, которая для обеспечения заднего хода опускается, перекрывает выходное отверстие насадки 9 и направляет струю по специальному каналу вниз и вперед, под нижний обрез транца. Благодаря тому, что насадка 9 имеет возможность поворачиваться относительно вертикальной оси и при закрытой заслонке, катер сохраняет способность управляться и на заднем ходу, хотя и с меньшим эффектом.
Обе основные детали РРУ — насадка и заслонка — изготавливаются из 2-миллиметровой листовой стали (желательно нержавеющей) с применением сварки. К насадке сверху приваривается поперечная планка-траверса, служащая для присоединения штуртросов и троса управления заслонкой реверса. Усилия, которые необходимо прикладывать к заслонке и поворотной насадке, сравнительно невелики, что позволяет для их привода применять тросик двойного действия («тяни-толкай») в оболочке. В этом случае рулевой трос присоединяют к одному из плеч траверсы, а второе остается свободным. Если же достать или изготовить такой тросик невозможно, то можно применить обычную штуртросовую проводку, присоединив концы троса к обоим концам траверсы, а середину закрепив на барабане штурвала. Отверстия диаметром 14 мм в траверсе служат только для облегчения конструкции.
Для уменьшения трения при повороте насадки в отверстия неподвижной насадки сопла под болты 11 можно запрессовать бронзовые втулки, между трущимися поверхностями обеих деталей поставить бронзовые же или латунные шайбы. Все гайки необходимо зашплинтовать или закернить.
На траверсе предусмотрено отверстие для крепления наконечника тросика управления реверсом. Напаянный на конец тросика шток 7 посредством вилки 4 и нагеля 16 соединен с изогнутым рычагом заслонки реверса 8. В случае, если тросик «тяни-толкай» отсутствует, можно применить простой гибкий трос диаметром 1,6—2,2 мм. Заслонка будет закрываться при натяжении тросика, а для ее возвращения в исходное положение (переднего хода) придется применить возвратную пружину. Это может быть пружина сжатия, поставленная на шток 7 между траверсой и рычагом заслонки, либо пружина растяжения, закрепленная одним концом к верхней кромке заслонки, а вторым — к специальному обушку на транце.
При изготовлении заслонки и насадки 9 по приведенным чертежам рабочий ход механизма привода должен составить около 30 мм.
Достать трос двойного действия на полную длину — от РРУ до пульта управления катером — довольно трудно, да и не обязательно. Снаружи на транце лодки можно установить достаточно простой исполнительный механизм, преобразующий горизонтальные перемещения обычного троса натяжного действия, проведенного с пульта управления через систему блоков, в вертикальные перемещения штока 7 Один из вариантов подобного механизма показан на чертеже РРУ. Сверху механизм закрывается легким кожухом из пластика.
Нечто подобное требуется сделать и для рулевого привода, расположив механизм в горизонтальной плоскости и соединив его штуртросами с барабаном штурвала. В месте прохода штока 1 сквозь транец придется поставить опору штока, которая обеспечивала бы ему небольшие угловые перемещения при перекладке руля с борта на борт. Разумеется, проход штока через транец нужно уплотнить мягкой манжетой, предотвращающей попадание в лодку воды, особенно при реверсе.
При испытаниях водомета обнаружится, что при поворотах и на заднем ходу масса водяных брызг вырывается из-под поворотной заслонки. Чтобы ограничить их распространение, рекомендуется выступающую за транец часть движителя закрыть сверху коробчатым кожухом из тонколистового металла или пластика. Кожух не должен мешать управлению катером, а его боковые кромки должны быть отогнуты вниз на 60—80 мм.
Короткий тросик двойного действия для привода реверсивной заслонки можно изготовить из стальной пружинной проволоки диаметром 1,8 мм, заключенной в обычную боуденовскую оболочку. При этом жесткость оболочки необходимо увеличить при помощи такой же проволоки, уложенной снаружи вдоль оболочки и прикрепленной к ней обмоткой двумя слоями изоляционной ленты. Конец проволоки припаивается к штоку, причем для надежности соединения проволоку нужно погрузить на глубину 10—15 мм в отверстие, просверленное по центру штока. В качестве штока можно использовать подходящую трубку.
Возможно применение и более простого РРУ с рулем, расположенным у внешнего торца неподвижной насадки цилиндрического или прямоугольного поперечного сечения. Такой руль достаточно эффективен на переднем ходу, а для реверса он разворачивается на 90°, перекрывая выходное отверстие и направляя струю в «носок» — вперед под днище катера. Разумеется, на заднем ходу катер с таким РРУ не управляем.
Установка двигателя
Для привода водомета «Мурены» можно использовать двигатель любого подвесного мотора мощностью свыше 20 л. с. (оптимальным является 30-сильный «Вихрь»), а также двигатели от тяжелых мотоциклов — при условии переделки их на водяное охлаждение и установки редуктора, снижающего частоту вращения гребного вала до 3000 об/мин. При большей частоте вращения КПД движителя будет очень низок, он не разовьет упора, необходимого для преодоления «горба» сопротивления. Особенно, если водомет будет устанавливаться на какую-либо заводскую лодку, имеющую большую, чем у «Мурены» смоченную ширину днища и массу.
Информация об изображении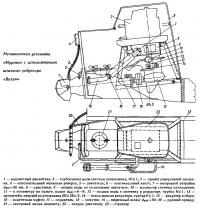
Механическая установка «Мурены» с использованием штатного редуктора «Вихря»
В качестве примера приводим общую компоновку двух вариантов механической установки с двигателями от ПМ.
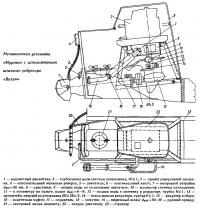
Механическая установка «Мурены» с использованием штатного редуктора «Вихря»
В первом варианте используется двигатель с поддоном и штатный редуктор ПМ, которые соединяются в единый агрегат через проставку 8 — коробку сварной конструкции из стали или легких сплавов. В верхней и нижней плитах проставки делаются отверстия для крепежных болтов поддона и редуктора для подвода (и отвода) воды в систему охлаждения двигателя вертикального вала и тяги реверса. Тяга реверса в данном случае может быть использована для разобщения двигателя с водометом только при его запуске, так как вода в систему охлаждения поступает только при работе ротора водомета — за счет напора около 1 м вод. столба, возникающего в потоке за ротором. От заборного штуцера, вмонтированного в сопло, вода по трубке 10X1 мм поступает в распределительный коллектор. От коллектора предусмотрены три отвода: на охлаждение двигателя, к змеевику, введенному внутрь корпуса редуктора для охлаждения масла, и к манометру низкого давления, установленному на пульте управления лодкой.
Вода из двигателя, пройдя рубашку глушителя, сбрасывается в газоводонепроницаемую нишу, вваренную внутрь проставки под выпускным окном поддона. Вода из змеевика редуктора может быть выпущена непосредственно за борт или, чтобы не делать лишнее отверстие в борту, — в глушитель 17, включенный в выпускной трубопровод. Нижний конец глушителя соединяется с выпускным патрубком в транце при помощи дюритового шланга, благодаря чему, а также впрыску воды в выпускной тракт, происходит заметное снижение шумности работы двигателя и вибрации, передающейся на корпус. С этой же целью, а также для компенсации неточностей центровки вала редуктора с валом движителя, соединение этих валов выполняется через муфту с эластичным элементом (см., например, стр. 343 третьего издания книги «15 проектов судов для любительской постройки», «Судостроение», 1985 г.).
Специальное внимание следует обратить на соединение коленчатого вала с вертикальным валом редуктора. В подвесном моторе погрешности центровки компенсируются за счет упругости довольно длинного торсионного валика — рессоры. В предлагаемой установке может быть применена короткая жесткая муфта, но при условии самой тщательной центровки обоих узлов. В противном случае для того, чтобы гарантировать достаточный ресурс установки, это соединение лучше выполнить также с упругим элементом.
Разумеется, полумуфты 16 должны крепиться к валам посредством таких же предохранительных штифтов, что и гребной винт на ПМ. Водомет не гарантирован от внезапного заклинивания ротора при попадании в водозаборник крупной гальки или какой-либо палки. Срезание штифтов в этом случае спасет двигатель от более серьезной неполадки.
Двигатель в сборе с проставкой и редуктором устанавливается на сварном кронштейне из металлических угольников, который опирается на продольные стрингеры корпуса и крепится к ним на болтах. Отцентровать установку с гребным валом можно за счет толщины прокладок, которые ставят между угольниками кронштейна и стрингерами, а также между кронштейном и поддоном двигателя.
Достоинством этого варианта является использование готового редуктора и двигателя без перестановки карбюратора, стартера, системы зажигания. Запуск и обслуживание практически не отличаются от обычного подвесного мотора. Используя гидрореверс, можно найти такое положение заслонки, при котором лодка будет стоять на месте с работающим двигателем. Запуск можно облегчить, открыв разгрузочный кран, сообщающий пространство водозаборника перед ротором с атмосферой (или же разобщив двигатель от водомета при помощи штатной нейтрали ПМ).
К недостаткам можно отнести необходимость введения змеевика для охлаждения масла в редукторе, некоторую потерю мощности за счет удаления настроенной системы выпуска отработавших газов, а также увеличенный по высоте габарит установки, вследствие чего капот двигателя выступает над палубой. Впрочем, от последнего недостатка можно избавиться, если наклонить двигатель на левый борт градусов на 60. Если карбюратор установить на проставке, сохраняющей вертикальное положение поплавковой камеры, то наклонное положение практически не скажется на работе двигателя.
Во втором варианте используется двигатель, отделенный от поддона и установленный горизонтально картером вниз. К фундаменту его крепят при помощи сварных кронштейнов — спереди за отверстия в проушинах под болты стартера и с кормы за четыре отверстия М8Х1,5, имеющиеся в нижней крышке картера (они снабжены стальными футорками, обеспечивающими прочность и долговечность резьбы). Для нормальной работы карбюратора его разворачивают на 90°; снимают с передней части двигателя высоковольтные трансформаторы и закрепляют их в более доступных местах. Фланец выпускного патрубка присоединяют непосредственно к выпускному отверстию штатного глушителя, подсоединяют к двигателю подвод и отвод охлаждающей воды.
Наиболее сложным узлом является редуктор с передаточным отношением около 1:1,7. Чертежи более или менее простой и компактной конструкции опубликованы в «КиЯ» №7 за 1966 г. Меж центровое расстояние этого редуктора 81 мм, в нем использованы косозубые шестерни с модулем 2,5 мм и шириной зуба 16 мм. Корпус и крышки фрезеруются из легких сплавов; снаружи корпус снабжается водяной рубашкой из тонколистового металла Редуктор может быть установлен вертикально или положен на бок, тогда ось коленвала двигателя оказывается смещенной от ДП лодки на 81 мм.
В заключение заметим, что автор и редакция с признательностью примут сообщения о подобных установках, выполненных в металле и испытанных на различных лодках, об усовершенствованиях конструкции и отдельных деталей, выполненных судостроителями-любителями.