Описываемая мотолодка, рассчитанная на 20-сильный мотор, несколько больше «Стрекозы»; она лучше приспособлена для прогулочно-туристских выходов, рыбалки и охоты на реках и малых водохранилищах, где нет волны. Практически плоскодонная, широкая в носу «Лотос-2» обладает высокой остойчивостью и хорошими скоростными качествами, малочувствительна к нагрузке. Мы ходим на ней с «Вихрем»: когда на борту лодки двое, скорость составляет 42 км/час, когда четверо — 35 км/час.
Основные данные лодки
Длина наибольшая, м | 4,04 |
Ширина наибольшая, м | 1,53 |
Ширина по скуле на транце, м | 1,48 |
Высота борта, м | 0,55 |
Вес корпуса, кг | 90 |
Лодка «Лотос-2» оборудована дистанционным управлением (мы убедились в том, что и на 4-метровых лодках это — вещь незаменимая); на оси рулевого колеса смонтированы рукоятки газа и реверса, а рядом — на переднюю панель вынесена кнопка «стоп». Под рукой у водителя к левому борту подвешена сумка для хранения документов, флага-отмашки и мелких вещей.
Для хранения запасов и походного снаряжения используются форпик (шп. 0—3), кормовой отсек (шп. 7—8), закрытый сверху дюралевым листом и отделенный от кокпита мягкой шторкой, а также сумки-карманы из павинола по бортам. Щиты пайола в р-не шп. 3—7 вырезаны из 6-миллиметровой фанеры.
Спереди кокпит защищен от брызг ветровым стеклом из плексигласа толщиной 8 мм, выполненным из отдельных кусков. На кромке палубы (по шп. 3 1/2) установлен поручень.
Края фальшборта по периметру кокпита защищены резиновым обделочным профилем, а бимс на шп. 7 — мягкой обивкой. Сиденьями служат четыре съемных мягких стула. Для удобства выхода и посадки пассажиров на носовую палубу уложен накладной лист с рифленой поверхностью.
Особенностью конструкции корпуса является то, что все продольные балки набора выполнены неразрезными и проходят снаружи обшивки. Это значительно упрощает дело, поскольку уменьшается число узлов пересечения продольного набора и шпангоутов. По существу только соединение днищевых ветвей шпангоутов с бортовыми на скуловом стрингере представляет некоторую сложность — приходится делать высадку на конце флортимберса.
О конструкции корпуса дают представление приводимые эскизы. Отметим лишь, что транец, обвязка которого собирается из угольников 25X25X2, дополнительно подкреплен: сплошным угольником такого же профиля, проходящим внутри корпуса от борта до борта на высоте привальных брусьев (перевязан с ними горизонтальными кницами); двумя наружными стойками (угольник 25X20X2) в плоскости ближайших к ДП днищевых стрингеров (перевязаны с ними вертикальными кницами), а также старнкницей в ДП. В районе крепления струбцин мотора поставлены деревянные подушки с обеих сторон транца: изнутри — от верхней кромки до горизонтального угольника, снаружи — как показано на эскизе.
Днищевые стрингера одновременно играют роль фальшкилей, а кроме того, в какой-то мере способствуют уменьшению брызгообразования и повышению устойчивости на курсе. Киль и первые от ДП стрингера проходят по всей длине днища вплоть до носовой кромки палубы, вторые от ДП стрингера заканчиваются в районе шп. 2.
Носовой кромкой корпуса служит горизонтально расположенная профилированная бобышка, выфрезерованная из дюралевого бруска 40X40X600. Листы обшивки и палубы крепятся к ней стальными самонарезающими винтами с установкой изнутри размалкованного по месту обделочного угольника.
При изготовлении набора были использованы следующие дюралевые профили; детали шпангоутов, привальные брусья, бортовые и палубные стрингера нарезаны из углобульба 25X20X2; скуловые стрингера — из угольника 30X30X2: киль и днищевые стрингера — из равностенного тавра 25X50X2. Планширь, имеющий вид угольника 90X18X2, был заготовлен из зетообразного профиля, у которого отрезана одна полка.
Кницы изготовлены из обрезков дюраля толщиной 2 мм.
Стыки наружной обшивки из дюраля Д16АТ (толщиной 1,8 мм на днище и транце; 1,2 мм — на бортах и 1 мм — на палубе) выполнены внахлестку на шпангоутах с прокладкой изолирующей ленты У20. Отметим, что в качестве прокладки могут быть использованы тиоколовая лента, полоски ткани, пропитанные грунтом АЛГ-1 или АЛГ-5, полоски полиизобутилена ПСГ миллиметровой толщины и т. п. Элементы основных заклепочных соединений показаны на эскизах; советы по выполнению холодной клепки легких сплавов можно найти в № 15 сборника, вышедшем в 1968 г. (подробнее — см. в книге А. Я. Розинова «Клепка судовых конструкций из алюминиевых сплавов», изд-во «Судостроение», 1964 г.).
Добавлю, что эксплуатация лодки уже в течение трех сезонов продолжительностью около семи месяцев каждый подтвердила правильность принятых нами конструктивных решений. На корпусе нет ни трещин, ни ослабления заклепок, ни каких-либо иных повреждений.
В заключение несколько советов по постройке дюралевых лодок вообще.
Первое, на чем я хотел остановиться, это выполнение конструкторско-подготовительной части работ. Дело в том, что при изготовлении металлического корпуса точность должна быть существенно выше, чем при работе с деревом, — тут шпангоут не подстрогаешь! Поэтому советую начинать с вычерчивания двух проекций теоретического чертежа (бока и плана) выбранной или спроектированной вами лодки в как можно большем масштабе (1:5; 1:2,5; 1:2). Это нужно для проверки плавности и согласования обводов и определения малок по шпангоутам. На этом чертеже, кстати говоря, желательно произвести и компоновку всего оборудования.
После уточнения плазовой таблицы, как обычно, вычерчивается на фанере проекция корпус — сечения по шпангоутам в натуральную величину. Надо нанести на плазовую разбивку положение теоретических линий (и закрасить сечения) продольных связей, а также очертания всех деталей (с учетом перекроев) шпангоутных рамок, включая флоры, бимсы, кницы-косынки, и провести линию пайолов.
Плаз полагается вычерчивать с точностью ±0,2 мм. Прямо по нему размечаются детали и собираются цельные шпангоутные рамки из заранее подогнанных и отмалкованных отрезков профилей.
Для мотолодок длиной до 5 м обычно применяются дюралевые листы толщиной: на днище 1,5—1,8 мм; на бортах 1,2—1,5 мм; на палубе 1,0—1,2 мм; на транце 1,8—2 мм. Использование больших толщин только приведет к необоснованному завышению веса корпуса без увеличения надежности и долговечности.
Стыки листов рекомендуется выполнять на наборе, разогнав их по длине так, чтобы стыки на днище не совпадали со стыками на бортах. Как общее правило, на стыках кормовая кромка одного листа должна накрывать носовую кромку другого, т. е. перекрои должны идти «по ходу» воды, обтекающей корпус.
Для изготовления деталей набора рекомендуются прессованные профили из Д16Т следующих сечений (не больше):
- угольники 30X20X2 (вес 1 пог. м — 0, 317 кг); 25X25X2 (0,275 кг); 30X30X2 (0,332 кг); 30X30X2,5 (0,411 кг); 40X40X2 (0,446 кг);
- углобульбы 25X20X2 (0,302 кг); 30X20X2 (0,331 кг); 25Х18Х1.5 (0,220 кг);
- Т-образные профили (тавры) 25X50X2 (0,427 кг); 35X40X2 (0,418 кг).
Листы и профили из Д16Т должны быть анодированы и загрунтованы. Если нет возможности анодировать материал, можно ограничиться грунтованием. Для этого предварительно необходимо тщательно обезжирить материал бензином «калоша» или Б-70, затем через 15—20 мин. — ацетоном за два раза с выдержкой 15 мин. Не позже чем через 15 мин. после обезжиривания надо покрыть листы и профили одним слоем грунта ГФ-032 или ФЛ-0В6.
Грунт ГФ-032 отличается высокими антикоррозионными свойствами и рекомендуется под масляные, пентафталевые, нитро- и перхлорвиниловые краски. Сушка при температуре 18—20° занимает 12 час.
Грунт ФЛ-0В6 по ГОСТ 16302—70 применяется при работе в пресной и соленой воде и рекомендуется под краски ПФ-223, перхлорвиниловые и нитрокраски. Режим сушки при 18—27° 6 час.
С целью обеспечения наибольшей прочности корпуса, упрощения конструкции и сокращения объема работы советую продольный и поперечный набор выполнять неразрезным. В конструкции «Лотоса-2» продольный набор вынесен на наружную сторону обшивки. Если это по каким-либо соображениям нежелательно, можно неразрезные стрингера установить и внутри корпуса, но появятся многочисленные узлы соединения их со шпангоутами. Не следует делать больше чем по одному стыку на стрингер; нельзя, чтобы стыки стрингеров лежали в одной плоскости.
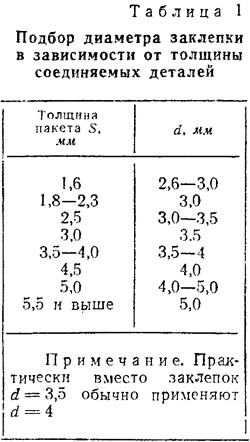
Швы по шпангоутам и стрингерам рекомендуется выполнять в один ряд заклепками диаметром 4 мм, шагом 30 мм, по скуловым и килевым профилям — такими же заклепками, но в два ряда в шахматном порядке с тем же шагом; палубу можно клепать заклепками диаметром 3 мм, шагом 25 мм. Привожу таблицу, которой можно руководствоваться при уточнении диаметров заклепок (табл. 1).
Если прочность какого-либо узла проверяется расчетом, надо считать, что при использовании материала Д18 усилие среза заклепки d=3 мм равно 134 кг, a d=4 мм 239 кг (при В65 в 1,3 раза выше).
Шаг по водонепроницаемым соединениям берется равным:
- по однорядным швам 3—4d;
- по двухрядным швам 6—7d в шахматном порядке.
Длина стержня заклепки при соединении двух деталей (двух толщин) определяется по формуле:

где S — общая толщина, а при клепке пакета из нескольких (трех и более толщин):

Клепку по соединениям набора и узлов оборудования рекомендуется производить заклепками с полукруглой или бочкообразной закладной головкой. Для уменьшения сопротивления движению днищевую обшивку в кормовой части лодки (глиссирующую площадку) лучше клепать заклепками с потайными закладными головками с наружной стороны; остальную часть обшивки днища, борта и палубу можно клепать заклепками с плосковыпуклыми полупотайными головками.
Информация об изображении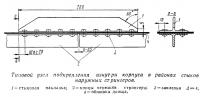
Типовой узел подкрепления изнутри корпуса в районах стыков наружных стрингеров
Перед сверловкой отверстий под клепку листы обшивки надо тщательно «обжать» — подтянуть к набору технологическими болтами с шагом не более 300 мм до криволинейных поверхностей и не более 500 мм на прямолинейных участках.
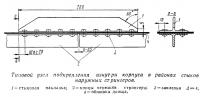
Типовой узел подкрепления изнутри корпуса в районах стыков наружных стрингеров
Для обеспечения прочности и герметичности диаметр сверла при подготовке отверстий надо брать на 0,1 мм больше, чем диаметр заклепки. После сверловки листы необходимо снять, чтобы удалить стружку и заусенцы, проложить по стыкам листов герметизирующую ленту. Отверстия под заклепки в ленте надо прокалывать шилом; сверловка после установки ленты недопустима.
На отверстиях под заклепки не должно быть граней, рваных кромок и трещин.
При клепке корпуса лодки чаще всего применяется так называемый обратный способ, при котором удары наносятся снаружи корпуса (ясно, что это удобнее, чем изнутри) по закладной головке (если она не плоская, то через обжимку с лункой по форме головки). Формируемая головка образуется при этом внутри корпуса за счет расплющивания конца стержня заклепки на массивной поддержке. Форму и размеры поддержки приходится выбирать по месту — в зависимости от удобства подхода к разбиваемому стержню заклепки. Привожу эскиз поддержки, при помощи которой было заклепано несколько различных дюралевых корпусов.
При соединении деталей шпангоутных рамок или иных предварительно изготовляемых узлов удобнее применять прямой способ клепки, когда удары наносятся по расклепываемому концу стержня заклепки.
Отмечу еще, что при проверке качества швов осмотром и простукиванием иногда приходится заменять дребезжащие, плохо поставленные заклепки; при этом диаметр заклепки нужно увеличить на 0,5—1 мм.
После окончания работ по изготовлению корпуса необходимо все заклепочные швы как внутри, так и снаружи лодки покрыть грунтом, после чего можно грунтовать весь корпус лодки. Окраску лодки и внутри и снаружи надо производить двумя слоями выбранной краски, например, водостойкой марки ПФ-223 или нитрокраски (ниже печатается небольшая заметка Б. П. Фаворова, расширяющая выбор грунтов и красок для покрытия новых дюралевых корпусов). Днище под пайолом желательно покрыть бензомаслостойкой краской.
Все стальные болты и детали должны быть кадмированными или оцинкованными, а затем загрунтованными и окрашенными.