Существующие гидравлические системы условно можно разделить на силовые и управляющие. Силовые гидроприводы, рассчитанные на передачу от ведущего элемента к ведомому большой мощности (например, передачу мощности от главного двигателя на гребной вал), на малых прогулочно-туристских судах встречаются крайне редко. А вот интерес к гидроприводам управления с каждым годом растет.
Чем же привлекателен гидропривод? Прежде всего — универсальностью: можно передавать как вращательное, так и поступательное движение. Насос может иметь как механический, так и ручной привод. Соединяется с исполнительным механизмом он не капризными и сложными в обслуживании механическими тягами, а гибкими шлангами, что значительно упрощает компоновку системы и ее монтаж на судне. На подвижные узлы исполнительного механизма можно передавать любую необходимую мощность без излишнего усложнения конструкции; в этом смысле гидропривод значительно проще, чем системы, в которых используются боуденовские тросы с гибкой оболочкой и различные карданные шарниры. Современный управляющий гидропривод обладает высокой надежностью, быстродействием, малой массой (масса гидродвигателя составляет 10—15% массы электродвигателя равной мощности).
В зарубежном мелком судостроении гидроприводы используются для дистанционного управления двигателем и реверс-редуктором, рулем, транцевыми плитами, дифферентом колонки, углом атаки подводных крыльев, заглублением подвесного мотора. При помощи гидравлики регулируют натяжение стоячего такелажа на некоторых крейсерско-гоночных яхтах. Как можно заметить, во всех этих случаях речь идет о передаче не вращательного движения, а прямолинейного, т. е. вперед-назад. Соответственно применяются при этом не гидродинамические передачи (с использованием гидравлической турбины — гидромотора), а гидростатические; механическая энергия потока преобразуется в них в механическую энергию ведомого звена при помощи поршня, движущегося прямолинейно в цилиндре.
Любой гидропривод состоит из насоса, подводящих жидкость трубопроводов и двигателя — гидроцилиндра, причем в качестве насоса и двигателя можно применять одни и те же поршневые механизмы. Так, для управления дроссельной заслонкой двигателя или редуктором чаще всего используются два совершенно одинаковых гидроцилиндра.
Рассмотрим одну из таких систем (рис. 1), применяемую для управления реверсом на крупных катерах. Первый — задающий — гидроцилиндр 3 расположен на пульте управления катером; он служит насосом. Исполнительный гидроцилиндр 6 является двигателем. При заполнении системы маслом запорные краны 2 открываются и масло из заправочного бачка 1, расположенного выше остальных элементов гидросхемы, самотеком поступает в обе полости обоих гидроцилиндров. Воздух при этом выпускают через клапаны 4, имеющиеся в верхней части каждого гидроцилиндра. (Подчеркнем, что отношение диаметра цилиндра к диаметру штока у обоих цилиндров должно быть строго одинаковым, так же как и объемы соответствующих полостей.)
Движение рычага управления на пульте вызывает перемещение поршня в задающем гидроцилиндре. Связанное с этим повышение давления в одной из ветвей трубопроводов перемещает в ту же сторону поршень исполнительного гидроцилиндра, приводя в действие механически связанный с ним рычаг переключения реверса.
Рассмотренная схема обладает обратной связью: поскольку к исполнительному механизму будет приложено усилие, такое же усилие на рычаге управления будет чувствовать рулевой (так же, как и момент срабатывания фиксатора в реверсе). Во многих случаях, например, для управления транцевыми плитами или дроссельной заслонкой, подобные схемы оказываются абсолютно неприемлемыми. Ведь необходимо не только повернуть ведомый элемент (например, транцевую плиту) на определенный угол, но и зафиксировать его в этом новом рабочем положении. Для фиксации ведомого элемента можно применить различные механические фрикционные стопора, однако наиболее целесообразным решением, особенно если необходимо воспринимать значительные нагрузки, будет установка запорного крана в одном из соединительных трубопроводов.
Удобны в эксплуатации, но и более сложны, схемы с гидравлическим замком (рис. 2). В корпусе 1 размещены два обратных шариковых (или, чаще, конусных) клапана, между которыми помещен плавающий поршенек 3. При перемещении поршня задающего цилиндра масло подается, например, через отверстие 4 в правую полость замка; в результате поршенек переместится налево и откроет левый клапан 2, соединив левые полости обоих гидроцилиндров. Далее, по мере повышения давления в той же правой полости замка, откроется правый клапан 5, и давление будет передаваться на поршень исполнительного цилиндра, вызывать его рабочий ход. Как только мы уберем нагрузку, оба обратных клапана замка автоматически под действием пружин закроются, надежно отсекая обе полости исполнительного цилиндра и фиксируя этим его поршень в заданном положении.
У этой схемы есть и минусы. Чтобы обеспечить срабатывание обратных клапанов, надо прикладывать некоторое дополнительное усилие. С течением времени в полости цилиндров со стороны штоков попадает воздух, связь становится «мягкой» — ручка управления пружинит, нарушается четкость фиксации. Кроме того, из-за неизбежных утечек масла рано или поздно нарушается точное соответствие положения поршней обоих цилиндров; в результате уменьшается ход исполнительного гидроцилиндра. Уменьшить вероятность попадания воздуха можно, установив дополнительный обратный клапан (5 на рис. 1), отрегулированный на минимальный перепад давления. Большое значение имеет качество работы.
При особо тщательном изготовлении деталей и монтаже необходимость в удалении воздуха и регулировке может возникнуть только через 30—50 ч работы гидросхемы; для управления реверсом, например, это соответствует десяткам тысяч включений.
В таких схемах, как управление воздушной заслонкой или приводом сцепления, достаточно иметь одностороннюю нагрузку на поршни, а возврат их в исходное положение осуществлять под действием пружин. Примером может служить привод сцепления легковых автомобилей. Поскольку жидкость при работе находится под давлением, попадание воздуха в систему практически исключено; при возвращении поршней в исходное положение происходит автоматическая дозаправка маслом. Подобные схемы практически не нуждаются в обслуживании.
Для натяжения стоячего такелажа на яхте (рис. 3) также может быть применена односторонняя схема. В этом случае, добавив клапаны 2 и 3 к задающему гидроцилиндру 1, получают простейший ручной насос, обслуживающий несколько силовых цилиндров 6. Манометр 5, установленный после двухходового крана 4, позволяет контролировать нагрузки на такелаж не только в момент регулировки натяжения, но и в процессе эксплуатации.
Информация об изображении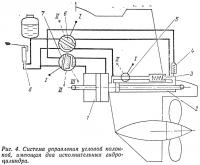
Рис. 4. Система управления угловой колонкой, имеющая два исполнительных гидроцилиндра
Схему с ручным гидронасосом можно использовать для подъема значительных тяжестей, например, для регулировки заглубления мощного подвесного мотора или наклона угловой поворотно-откидной колонки. Отличие механизма для подъема и регулировки положения колонки состоит в том, что он должен удерживать колонку с постоянным (хотя и относительно небольшим) усилием. Это необходимо для того, чтобы при резком уменьшении числа оборотов поток воды не мог отбросить ее от транца на переднем ходу и в нейтральном положении, чтобы амортизировать удар колонки по транцу после откидывания и жестко фиксировать колонку .при включении заднего хода.
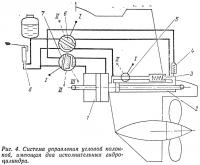
Рис. 4. Система управления угловой колонкой, имеющая два исполнительных гидроцилиндра
Наиболее полно удовлетворяет всем этим требованиям схема, включающая два цилиндра (рис. 4 и 5). Цилиндр 1, имеющий большой диаметр и малый ход, предназначен для регулировки на ходу угла наклона оси гребного винта колонки с целью получения оптимального дифферента и максимальной скорости. Цилиндр 2, имеющий малый диаметр и большой ход, обеспечивает подъем колонки. В реальных конструкциях чаще применяется схема с двумя одинаковыми цилиндрами подъема, расположенными с обеих сторон колонки. При обычной эксплуатации катера кран 6 установлен в положение II. Колонка удерживается от откидывания за счет повышения давления в правой полости цилиндра 2. При наезде на препятствие давление в этой правой полости резко повышается, в результате срабатывает предохранительный клапан 3 и масло из правой полости перетекает в левую (давление открытия клапана регулируется натяжением пружины). После прохождения препятствия под действием веса и упора работающего винта колонка возвращается в первоначальное положение; при этом масло попадает в правую полость цилиндра через обратный клапан 4. Следует отметить, что откидывание колонки происходит за очень короткий промежуток времени, поэтому проходное сечение клапана 3, крана 5 и соединяющих трубопроводов должно быть достаточно большим, чтобы исключить чрезмерное повышение давления в гидроцилиндре 2. При включении заднего хода тяга механизма реверса перекрывает кран 5 (положение II), благодаря чему исключается возможность откидывания колонки.
Как подъем колонки, так и регулировка ее угла наклона производится ручным насосом 8, который при помощи кранов 6 и 7 подключен к соответствующим исполнительным гидроцилиндрам.
Основу всех рассмотренных схем составляет гидроцилиндр. Представление об устройстве исполнительного гидроцилиндра одностороннего действия дает рис. 6. Для уплотнения подвижных соединений наибольшее распространение получили резиновые кольца круглого сечения, что позволяет существенно упростить всю конструкцию цилиндра. Долговечность его достигается изготовлением штока и цилиндра из качественной стали с последующим хромированием или из нержавеющей стали; иногда применяют латунь либо (наихудший вариант) анодированный дюралюминий. Поршень и направляющие втулки изготовляют из более мягких металлов — бронзы, силумина, алюминиевого сплава АМг. Наиболее распространенная посадка в соединениях Н9/f9 (А3/Х3), чистота обработки Ra=0,32—0,63 (для деталей из цветных сплавов Ra=1,25—0,63). Глубину канавки делают на 7—12% меньше диаметра сечения уплотняющего кольца, ширину — на 25—30% больше.
В тракторостроении применяют унифицированные гидроцилиндры ЦС с ходом поршня до 200 мм и диаметрами 36, 55, 75 мм и более. Максимальное давление жидкости в гидроцилиндрах обычно в пределах 100—150 кгс/см2; рабочее, обеспечивающее достаточно высокие КПД и ресурс, 50—75 кгс/см2.
Естественно, наиболее удобны системы управления, в которых вместо ручного насоса применены насосы с механическим приводом от главного двигателя или электродвигателя. Наиболее распространенным вариантом является шестеренный насос (рис. 7, а). Номинальное число оборотов такого насоса должно обеспечивать окружную скорость шестерен, равную 5—6 м/с. КПД насоса зависит от утечки жидкости через осевые и торцевые зазоры. При снижении числа оборотов насоса теоретический расход жидкости уменьшается, в то время как утечки остаются постоянными. При значительном уменьшении частоты вращения теоретический расход и утечки могут сравняться, действительный расход будет отсутствовать. Число оборотов, соответствующее нулевому расходу при номинальном давлении, которое указано в паспорте насоса, составляет 10—20% номинальной частоты вращения. При уменьшении давления число оборотов нулевого расхода уменьшается пропорционально: так, если насос развивает давление 25 кгс/см2 при номинальном давлении 150 кгс/см2, число оборотов, при котором расход уменьшится до нулевого, составит всего 2—3% номинальной частоты вращения.
В некоторых современных насосах для автоматического уплотнения шестерен по торцам применяются специальные втулки, которые поджимаются давлением жидкости. У этих насосов обороты, которые соответствуют нулевому расходу, составляют 5—8% номинальных. Существенный недостаток шестеренных насосов с автоматическим уплотнением — возможность вращения только в одну сторону.
В тракторостроении применяется ряд шестеренных насосов НШ-6, НШ-10, НШ-32 (цифры в обозначении характеризуют рабочий объем — объем жидкости в см3, подаваемой за один оборот вала без учета утечек). Эти насосы с автоматическим уплотнением имеют номинальное давление 100 кгс/см2 и номинальное число оборотов 3000—1800 об/мин. Высокая износоустойчивость позволяет навешивать их непосредственно на главные двигатели, что обеспечивает постоянную готовность насоса к работе (естественно — при работающем двигателе).
Насосы имеют небольшие габариты и вес; так, габариты НШ-10, рассчитанного на передачу мощности до 8 л. с., всего 90X115XI00 мм, вес 2,5 кг.
В других отраслях промышленности применяют шестеренные насосы с меньшим рабочим объемом 0,5—3 см3/об, приводимые от электродвигателей постоянного тока напряжением 27 В (вполне удовлетворительно они могут работать и при напряжении 12 В).
Мощность, необходимая для привода, нередко оказывается очень малой. Например, для подъема угловой колонки за 60 с достаточна мощность 25 Вт. Другими словами, для этой цели можно использовать 12-вольтовые двигатели от вентилятора «ВАЗ-2106» или двигатели от отопителей автомобилей «ВАЗ». Однако подобрать насос на такой небольшой расход удается не всегда. В таких случаях насос соединяют с двигателем через понижающий редуктор. Во избежание резкого понижения КПД число оборотов насоса должно быть в 2—3 раза выше числа оборотов нулевого расхода при соответствующем давлений.
Рабочее давление и КПД у пластинчатых насосов (рис. 7, б) обычно несколько ниже, чем у шестеренных. Пластинчатый насос используется, например, для привода гидроусилителя руля автомобилей «ЗИЛ»; в промышленности широко применяется насос 5БГ.
Наиболее сложную конструкцию, но зато и максимальный КПД (0,8—0,9) имеют аксиально-поршневые насосы (рис. 7, в). Их рабочее давление доходит до 200—300 кгс/см2 (обороты нулевого расхода составляют 3—4% от номинальных).
Если гидронасос работает от основного двигателя, для управления гидроцилиндром можно применять тракторные распределители типа Р 75-В. Такой распределитель имеет четыре положения: плавающее, когда обе полости цилиндра соединены со сливной полостью; нейтральное, когда обе полости отсоединены от гидросистемы; положение подъема и опускания. Если при подъеме и опускании поршень доходит до крайнего положения, давление в гидросистеме поднимается; как только оно достигнет 125 кгс/см2, срабатывает специальный запорный клапан, рычаг распределителя автоматически переводится в нейтральное положение. Если гидронасос работает от электродвигателя, то при подходе поршня к крайним положениям двигатель выключается за счет срабатывания концевых выключателей.
Гидросистемы управления рулем могут иметь как простейший ручной, так и механический привод, в том числе и привод от главного двигателя. Соединив штурвал (рис. 8) с задающим гидроцилиндром при помощи червячного (рулевой механизм от легкового автомобиля) или двухступенчатого цилиндрического редуктора, получают схему, аналогичную показанной на рис. 1. В отличие от механических, гидравлические схемы рулевого управления позволяют осуществлять очень жесткую (практически без люфтов) связь штурвала с рулем даже при большом удалении их друг от друга. Ясно, что подобные схемы очень чувствительны к качеству изготовления и монтажа, а также требуют эпизодического обслуживания в связи с необходимостью удаления воздуха.
В схеме, показанной на рис. 9, вращение штурвала 1 через повышающую зубчатую передачу 2 передается на вал реверсивного гидронасоса 3, соединенного трубопроводами с силовым исполнительным гидроцилиндром 6. Для того чтобы при повороте штурвала на одинаковый угол вправо и влево угол поворота руля 7 также был одинаковым, применяется поршень с двумя штоками.
Если насос соединить непосредственно с гидроцилиндром, руль, выведенный из среднего положения, из-за утечек через насос будет медленно возвращаться в среднее положение даже при неподвижном штурвале. Чтобы этого не происходило, приходится устанавливать гидрозамок 5, конструкция которого была рассмотрена выше. После остановки штурвала гидрозамок срабатывает и отключает гидроцилиндр от насоса, поэтому нагрузки от руля на штурвал не передаются. Для компенсации возможных утечек жидкости применяются шариковые обратные клапаны 4. Система очень надежна и практически не нуждается в обслуживании, что и обусловило ее широкое применение на больших прогулочных яхтах. Однако управление катером или яхтой, оборудованными такой схемой, имеет свои особенности. Например, при очень медленном повороте штурвала руль поворачиваться не будет из-за утечек в гидронасосе. Штурвал надо поворачивать чуть резче обычного; при этом нужно преодолеть начальное усилие, необходимое для открытия гидрозамка. Опять же из-за утечек положению «прямо» руля с течением времени будут соответствовать разные положения штурвала.
Управление пером руля по схемам 8 и 9 имеет общий недостаток: при резкой переброске штурвала увеличение скорости течения жидкости в трубопроводах приводит к возрастанию потерь на трение и заметному увеличению усилия на штурвале, причем эта особенность проявляется, даже если руль отключен от гидроцилиндра. Чтобы этот минус проявлялся не слишком заметно, внутренний диаметр трубопроводов должен составлять не менее 18—20% диаметра цилиндра.
Обычно в гидросистемах применяют масла, используемые для смазки двигателей. Однако для схем с ручным управлением целесообразно уменьшить вязкость масла, разбавляя его соляром, либо использовать веретенное масло или специальную жидкость для гидросистем АМГ. Естественно, что утечки при атом увеличиваются.
Информация об изображении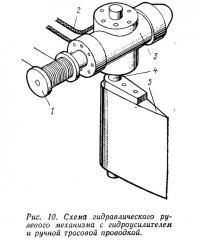
Рис. 10. Схема рулевого механизма с гидроусилителем и ручной тросовой проводкой
В настоящее время разработано немало различных систем управления рулем, в которых благодаря применению привода насоса от главного двигателя или от специального электромотора удается резко снизить усилие на штурвале. Схемы эти довольно сложны, поэтому, на наш взгляд, при постройке малых судов целесообразнее пользоваться хорошо отработанными конструкциями таких рулевых механизмов, установленных на колесных тракторах и автомобилях «ЗИЛ».
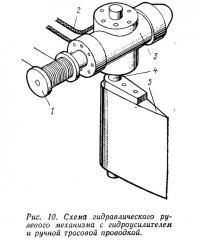
Рис. 10. Схема рулевого механизма с гидроусилителем и ручной тросовой проводкой
Руль 5 (рис. 10) крепится к валу сошки 4. Непосредственно в рулевом механизме имеется исполнительный гидроцилиндр-усилитель 3, к которому подсоединяются трубопроводы 2 от гидронасоса. Усилие от штурвала передается на вал червяка 1 либо обычной тросовой передачей, либо системой валиков. Данная схема позволяет управлять рулем даже при неработающем гидронасосе (естественно, усилия на штурвале при этом резко возрастают и оказываются даже несколько большими, чем при обычной механической передаче, за счет перекачки масла в гидроцилиндре).
Малый вес и простота управления позволяют использовать серийные гидронасосы для привода подруливающих устройств, аварийно-вспомогательного движителя, для запуска одного двигателя от другого. При мощности главных двигателей до 50 л. с., используя те же серийно выпускаемые узлы, можно осуществить и гидравлическую передачу на гребной винт. Однако в принципе такая силовая установка с гидропередачей оказывается тяжелее обычной: пониженный КПД потребует установки в 1,5 раза более мощного двигателя (естественно, возрастает и расход топлива).
Расчет некоторых элементов механизированных гидроприводов
Зная номинальное число оборотов (nн, об/мин) и рабочий объем (V, см3/об) имеющегося насоса, а также диаметр (d, см) и ход (h, см) поршня исполнительного гидроцилиндра, определим время его полного хода по формуле:
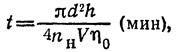
где η0 принимается равным 0,9—0,95 при номинальных оборотах гидронасоса, уменьшаясь до 0,5 — при пониженных.
Мощность, необходимую для привода гидронасоса, можно вычислить по выражению
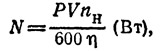
где КПД гидронасоса η принимается равным 0,7—0,8 при номинальных оборотах гидронасоса, уменьшаясь до 0,25—0,3 при пониженных; Р — рабочее давление, кгс/см2.
Основные параметры гидросхемы рулевого управления, представленной на рис. 9, рассчитывают в такой последовательности.
1. Определяют передаточное отношение от штурвала к гидронасосу:
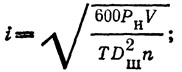
при i<1 — передача повышающая, при i>1 — понижающая. Здесь n — расчетное число оборотов гидронасоса (в первом приближении его можно принять в 2—2,5 раза больше числа оборотов нулевого расхода при номинальном давлении); T — усилие на штурвале (6÷10 кге); DШ — диаметр штурвала, см; РН — номинальное давление гидронасоса, кгс/см2.
2. Определяют рабочее давление, развиваемое гидронасосом:
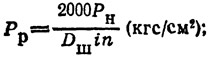
если РP < 20 — привод будет иметь большие габариты и низкий КПД; при РP>70—80 целесообразно увеличить i. Явное преимущество имеют аксиально-поршневые гидронасосы с рабочим объемом около 5 см3.
3. Определяют диаметр поршня исполнительного гидроцилиндра:

принимая k=0,2 для небалансирного пера руля, k=0,08 — для балансирного; h — ход поршня 15—25 см; v — скорость судна, м/с; FP — площадь пера руля, м2; ВP — средняя ширина пера руля, см.
4. Определяют число оборотов штурвала при перекладке пера руля от положения в ДП на максимальный угол (около 45°):
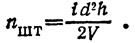
Если nШТ окажется меньше 2—2,5,то целесообразно увеличить d. При малой скорости вращения штурвала за счет утечек число оборотов может быть большим.